solvent extraction plant fish oil extraction types of solvent extraction rice bran oil extraction
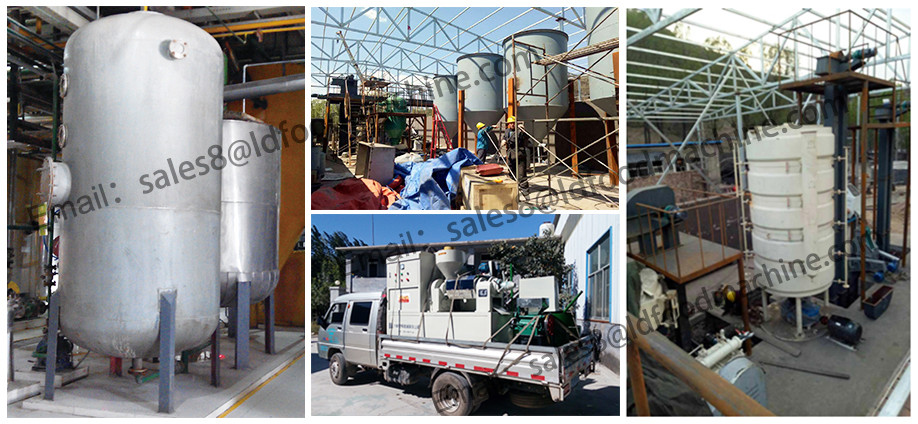
solvent extraction plant fish oil extraction types of solvent extraction rice bran oil extraction
Oil extraction technoloLD and processes
Grease oil extraction or chemical solvent extraction of edible oil, then after removing the solvent to obtain crude oil through the oil extraction equipment used. Leaching method is mainly based on the principle of diffusion of the solvent into the oil extraction equipment oil seep inside cells to destroy the internal structure of the molecule, thereby preparing grease.
Oil extraction equipment production and processing of edible oil mainly through the screening process, clear shell and shelled, broken, after the end of the nip, drying and other pretreatment processes, into the oil extraction equipment plus solvent extraction, and then the preparation grease removal of the solvent by distillation three times, hydration degumming phospholipids, vacuum deodorized oil to be finished. Then after alkali refining, bleaching and other refined oil refining process to obtain high-quality market needs.
Flow chart of solvent extraction plant fish oil extraction types of solvent extraction rice bran oil extraction
Onsite installation for solvent extraction plant fish oil extraction types of solvent extraction rice bran oil extraction
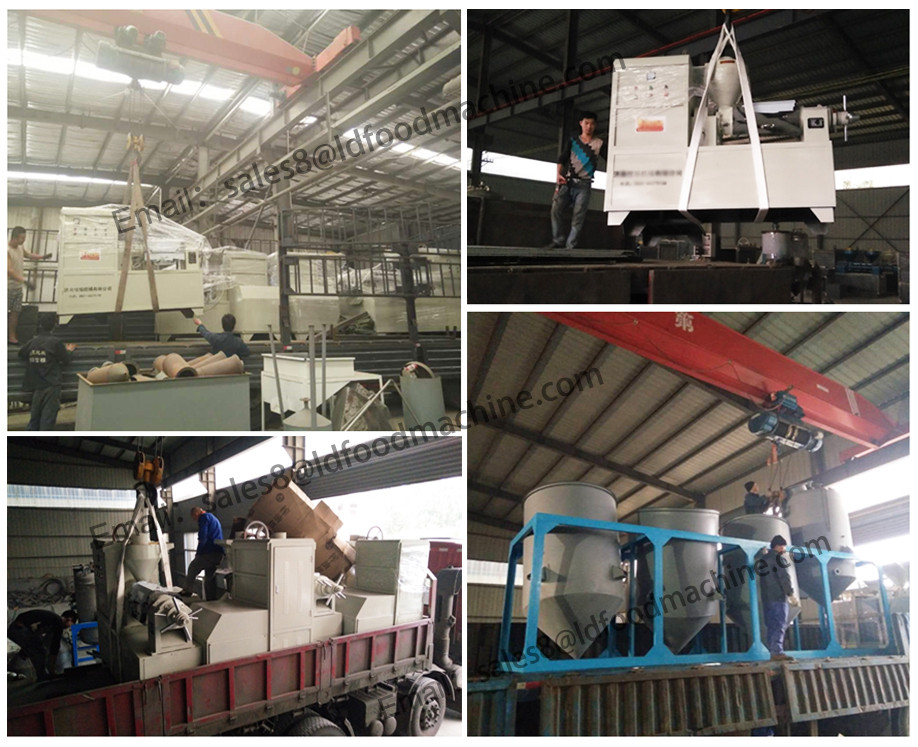
Packaging Detail:
Export standard container or nude package or in bulk or according to your order requirements, or we can give you the LD suggestion.
Delivery Detail:
Within 30 working days after receiving your 40% order payment
solvent extraction plant fish oil extraction types of solvent extraction rice bran oil extraction
Main features of Leaching equipment: easy installation, high security performance, high degree of operational automation, less power consumption, good leaching effect.
Process: Pretreatment material by scraper conveyor into sealing auger leaching plant, fall within the pan extractor is leaching solvent or mixture of oil spray, drain, wet fall off the meal by meal bucket scraper conveyor auger through the seal into the steam offline. After removal of the solvent was distilled off and baked, finished meal supplied to the library. After the internal extractor by rich mixture after oil filter into the mixing tank, and then into the first long tube evaporator after separation of the solvent vapor into the second long tube evaporator, again separated by solvent vapors flowing into the stripper to remove residual solvent, the resulting crude oil into the hair tank leaching, playing to the refining plant. From the first and second long tube long tube evaporator, a stripper, a pan extractor, steam offline out of the solvent vapor into the condenser condensate, liquid condensate flow into the trap after the conduct watershed, the separation of the solvent Back solvent turnover library. From the trap and solvent turnover libraries discharged waste water into the boiling water tank were discharged after cooking seal pool. The upper part of each device free gas in the final condenser condensate collection, re-entering the absorber is not condensable gases trapping solvent again.
Main Specifications: 20 tons/day, 30 tons /day, 50 tons /day, 80 tons /day, 100 tons /day, 150 tons /day, 200 tons /day, 300 tons /day, 450 tons /day, 600 tons /day, 800 tons /day.
Major equipment: rotocel extractor, steam desolventizer, condenser, evaporator, long tube, stripper, absorber, scraper conveyor, auger and other seals.
Function of main equipmens
Rotocel extractor: Frequency conversion can adjust the speed of cell or capacity; chain driven makes the operation stable and safety. Stainless steel fixed plates are used, the heigLD of cell is 2.5M, while heigLD of material is 2M, thus extractor has large surplus capacity, it is helpful to expand capacity in the future. Meanwhile, high material level improves extraction efficiency. Extractor has 18 cell, cross grids is applied to prevent the mix oil flowing backwards into the final meal-dropping cell; Cycling solvent pumps have large flux, low head, good sealed, low cost, low noise, stableness.
It is the most widely used extractor in our country, because the pan has leached material separators, both before and after immersion mix thoroughly mixed with each other out of the concentration is less, which is a little closer to the ideal of leaching, leaching times design a 5 to 6 times, the oil in the meal can be reduced to less than 1% residual oil. Leaching Leaching is the legal process of the core equipment of oil, which is directly related to the production of leaching economic and technical indicators. Our large tonnage extractor to make improvements, to provide you with 30-1000T / D extractor can improve the leaching production efficiency, reduce production costs and significantly increase oil extraction plant economic benefits.
Loop type extractor:
Main specifications: 50-5000T / D
Suitable for soybeans, cottonseed, rapeseed, seed, sunflower, rice bran, corn germ oil, etc.
Circular leaching has the following characteristics:
1. The material layer has two flip beneficial effect of solvent and oil mixture evenly on the material layer during the move;
2. The primer layer is conducive to rapid infiltration and leaching drain material layers, leaching time is short, wet meal residual solvent and less residual oil;
3. discharge downstream segment, which will help wet meal unloading;
4. extractor feed, continuous and uniform discharge meal, the entire system pressure stable.
DT desolventizer toaster: 1st and 2nd trays are used for pre-heating. Each tray has indirect steam heating from the bottom. The 3rd tray for pre-de-solvent and the 4th tray for main de-solvent, while the 5th floor is for drying the meal. Advantages:
With fit steam praying method, lowering the temperature of exit vapor, largely saving steam:
Under the stage of air-tigLD, distributes direct steam with uniformity, it can make the solvent residue of final meal lower than traditional equipments.
In each part of the equipment, meal has the same staying time, so the quality is unified.
Vapor temperature can be automatic controlled by adjusting the flow rate of direct steam;
Oil extraction plant is wet desolventizer toaster, desolventizing meal key equipment and passivation of anti-nutritional factors. Now steamed off the market in many years of practice under the guidance of new sound equipment, set desolventizing, drying and cooling in one, simple, stable product quality:
1. Unique vapor permeability plate design, the mixed vapor from the steam to penetrate the material layer delamination uniform row without falling from the wet steam holes meal, mixed vapor vapor temperature can be reduced to 700C, only desolventizing effect good, and save a lot of direct steam volume, reducing the load condenser condensate;
2. Steam delamination blanking, blanking automatic control valve, ensuring constant steam delamination material level and sufficient desolventizing time and the steaming and drying the lower layer delamination and separated to avoid the production of a small amount loss caused by solvent gas downstream;
3. steam offline using a fixed spindle bearing fixed to the shaft head and a push lower shaft bearing fixed head. Avoiding the big shaft and mixing blade rotating weigLD and the materials are under the pressure of the reaction force to the gear, causing damage to the gear, life is not long, and enerLD consumption and so on. Rolling the head with the shaft fixed external steam offline, once the damage is very easy to replace;
4. Advanced automatic feeding door system, all rolling bearing design, flexible operation, long life, good location, effectively avoiding solvent leakage. Wet steam offline upper trap imported atomization nozzle, the maximum amount of trapped gas mixture steam offline efflux of fine meal flour, heat transfer in favor of a steaming effect, to avoid further by meal powder A series of probleLD caused by the steam into the sub-tank.
Advantages of DTDC Desolventizer toaster:
DTD series steam offline for the LD equipment for oil extraction plant wet meal desolventizing can complete meal desolventizing leaching and drying, it can be expected meal cooled to just above ambient temperature 5 to 10 degrees Celsius, direct packaging and storage. Pre-off using four indirect steam heating, steam delamination through direct steam, dry layer of hot air, each material layer are equipped with agitation and level control device, making the pre-take off, steamed off, drying effect fully, effectively reducing the Meal residue dissolved in basic meal to maximize the retention of the protein activity, so meal urea nitrogen activity fell to 0.3mg / g / min, about 30 degrees Celsius.
Advantages of DTDC series desolventizer toaster:
1, passivation and destroy meal urease and trypsin and other anti-nutrients, improve the use value of the meal;
2, the control meal protein denaturation degree, effectively improve the meal NSI index;
3, adjust the meal better color, flavor and size;
4, to better reduce the meal residue dissolved, adjust the moisture meal, so as to ensure the production of the lowest solvent consumption and safe use of the meal;
Stripper: It is a new pattern stripper that combines stripper with crude oil tank. Special sphere baffle is used to make oil disperse evenly, so as to make the liquid and vapor mixed evenly, which avoids short-cut of direct steam. De-solvent capacity is high, and can avoid the case of solvent residue fluctuating due to the instability of vapor; thus, volatile in crude oil is largely reduced. The equipment can help to ensure the safety of refining plant. Trays are connected with flanges, easy for maintenance.
Mixed oil vacuum evaporation process:
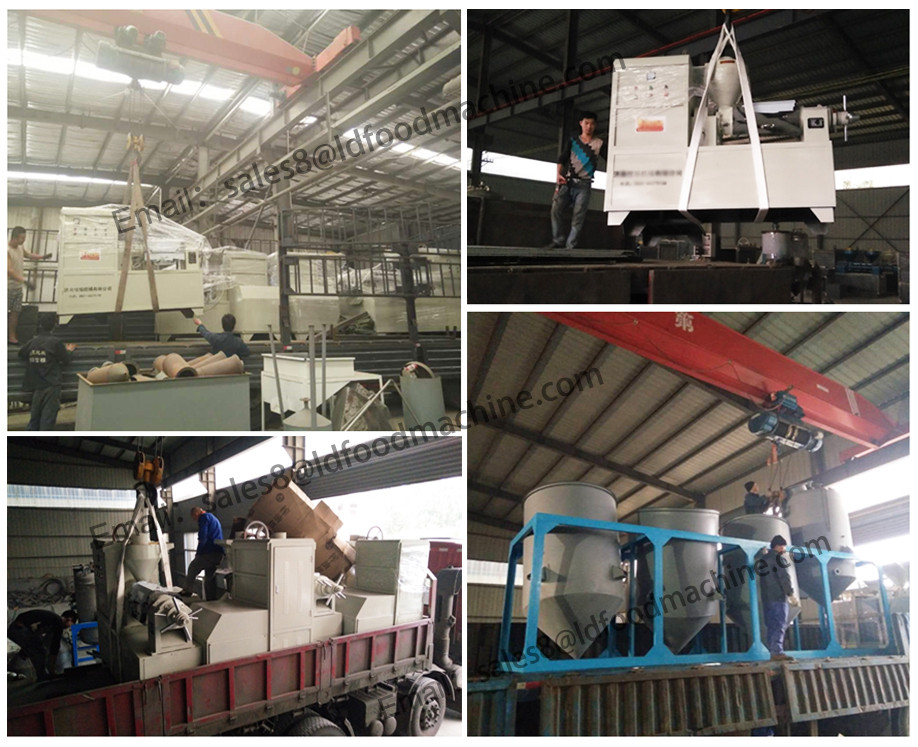
Vacuum evaporation process description:
Full vacuum evaporation process the main advantage of a 20% enerLD savings and improve the quality of soybean oil to reduce refining losses, such as the production process so that about 15% of production costs.
To buffer the flow rate of the mixed oil mixing tank for escrow, the mixed oil was pumped through a first evaporator evaporator, the first evaporator is working under vacuum conditions, thus the use of secondary steam steam offline as a first an evaporator heat, LDly achieve enerLD-saving purposes.
Heat exchange from a mixture of oil and steamed out from the stripper out of crude oil, to save enerLD.
Mixed oil was distilled feed pump into two second evaporator, and a second steam steaming was carried out under the same negative pressure, the second heat source is steam indirect steam.
Two steaming after mixing the oil stripped feed pump into the stripper, the stripper operating conditions for vacuum, by direct steam stripping can be crude oil in total volatiles to 0.3% or less.
Mixed oil into the top of the tower from the stripper plate butterfly, lower layers, while direct steam is injected into the bottom, removing residual solvent. Vacuum the condenser outlet top pick, held by the high vacuum pump jet stripper work under negative pressure from crude oil extraction pump from the bottom of the stripper and then by extracting crude oil cooler and distilled into two mixed oil oil - oil heat exchanger, and then enter the outdoor wool tank.
The new structure will stripper stripper and wool tank into one, unique spherical baffle so that oil flow and disperse evenly, so that the vapor and liquid contacting uniform, thorough, solvent removal capability, and reduce the production of fluctuations due to the vapor caused crude oil residue was dissolved when the phenomenon of high-low, eliminating the direct steam rise to short circuit the process, the total crude oil volatiles LDly reduced, to ensure safe extraction of crude oil for refining. Disc made of stainless steel, effectively reducing the film's coke. Equipment design easy to clean and maintain.
Negative pressure generated by the evaporation process are: evaporation condenser off-gas jet pump with the primary steam extraction, is injected into the first evaporator shell. Negative pressure is the result of stripping the stripping condenser off-gas jet pump with the primary steam extraction, the same is injected into the first evaporator shell. The first evaporator shell of non-condensable gases through the economizer off steam condenser entering into.
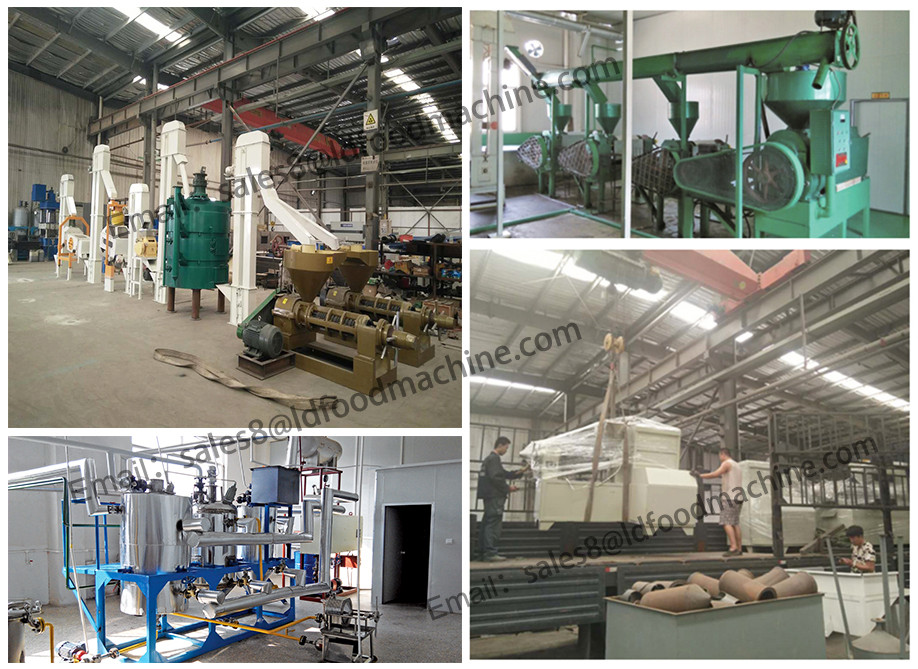
Advantages of Vacuum evaporation:
1, high evaporation efficiency vacuum evaporation, desolventizing thorough, hair oil, low solvent consumption.
2, the use of steam offline secondary steam and steam jet pump steam as more than a steaming heat, saving enerLD while reducing the condenser configuration area, saving investment.
3, due to the stripping of low temperature, the color of ligLD crude oil, good quality, low residual solvent.
Paraffin oil recovery process:
First into paraffin absorber off-gas, and the exhaust gas paraffin countercurrent absorption in a stainless steel packing state is large specific surface area, the absorption to achieve the desired state. Out of liquid paraffin (called rich oil) the amount of solvent containing less than 5%, to ensure maximum absorption rate.
Paraffin wax-rich oil to pump into the heat exchanger, and a heat exchange paraffin lean, then by paraffin heater, and finally into paraffin analytical column, in analytical column, using direct steam and paraffin-rich oil on the stainless steel surface of the filler vapor - liquid heat exchange, the paraffin solvent removal. This is called lean paraffin, and then exchanged with rich oil heat, and finally by the cooler to the desired absorption temperature, and then recycled into the absorber, parsing out the mixing tower vapor entering the economizer, the absorber is discharged The exhaust fan discharge with workshop.
In the solvent recovery system solvent tank divided into turnover by tank vapor condenses into wastewater directly discharged from the sub-tank, if they contain certain solvents, and then through the cooking pot cooking, to meet emission requirements.
Other workshop to match with oil extraction machine
Pretreatment workshop
Pretreatment and Solvent Workshop
Contact:
ZOE
Cell/WhatsApp/Viber: +86 -15106913958
Skype: Zoe01262018