LD'e fabricator 2015 new condition soya oil extraction plant with engineer group
LD'E MAIN BUSINESS SCOPE:
10-500T/H oil material first cleaning,drying and storage section turn-key project;
100-3000 T/D oil pretreatment, shelling and pre-press workshop turnkey project (soybean hot peeling, bean skin crushing; the soybean extrusion, high oil contained pre-press cake extrusion, and high oil contained embryos puffed; of direct puffed). Rice bran production line turn-key project;
100~300TPD Leachingworkshop turnkey project (Towline extractor, Rotocel extractor, loop type extractor, DTDC separated machine, the full negative pressure evaporation, paraffin wax recovery, leaching workshop degum, phospholipid concentrate);
30-1000T/D oil continuous grade one or two physical (chemical) refining production line;
20-3000T/D sunflower oil, rice bran oil, corn germ oil dewaxing turn-key project;
10-200T/D Fatty acid esterification production cooking oil production line.
BRIEF PROCESS OF SOLVENT EXTRACTION SECTION:
Material embryos→Extraction→Wet meal→Evaporation→Cooling→Product meal
↓
Mixed oil→Filter→Negative pressure evaporation → Crude oil
↓
Solvent recovery
WHAT IS SOLVENT EXTRACTION MACHINE LIKE?
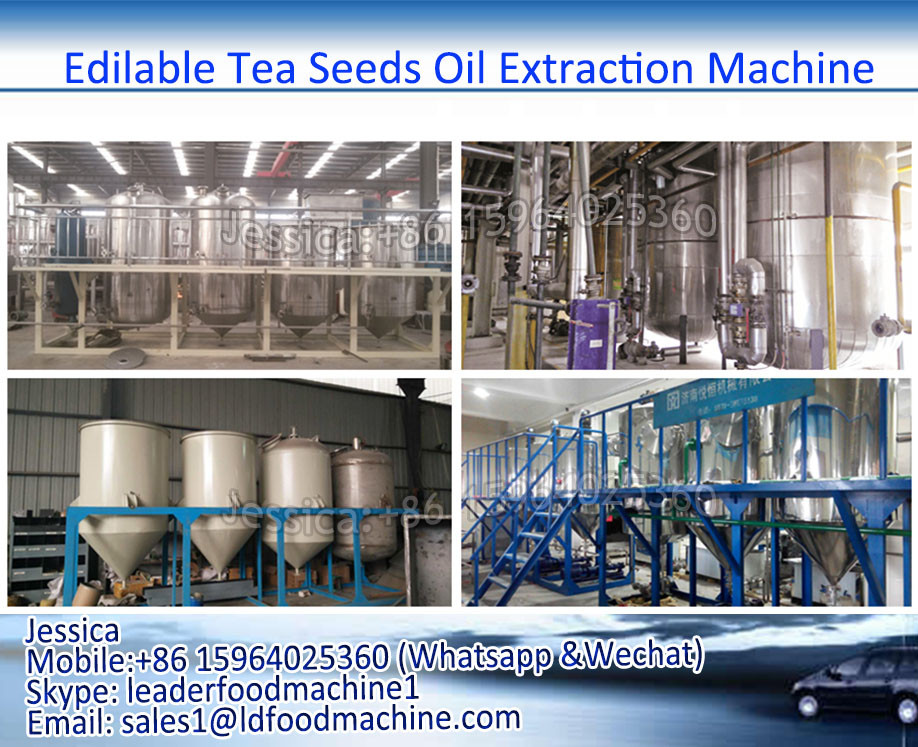
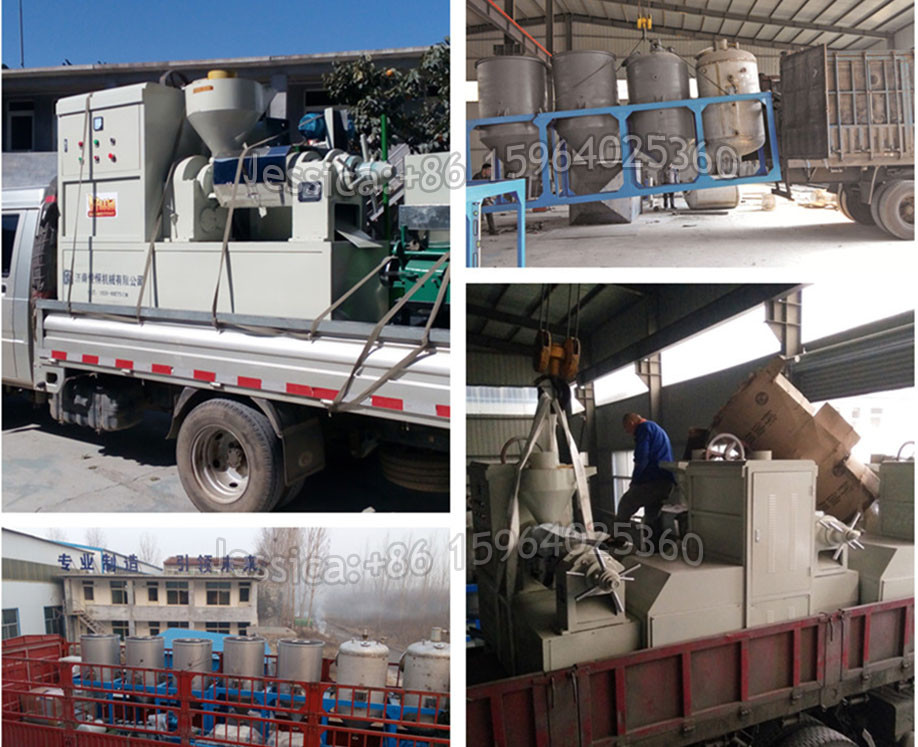
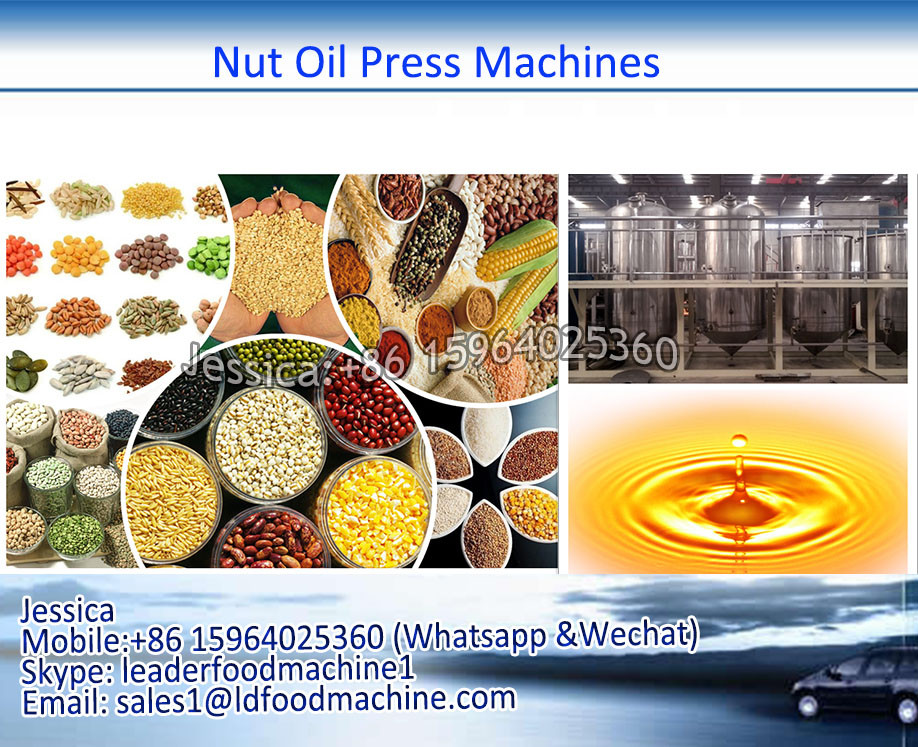
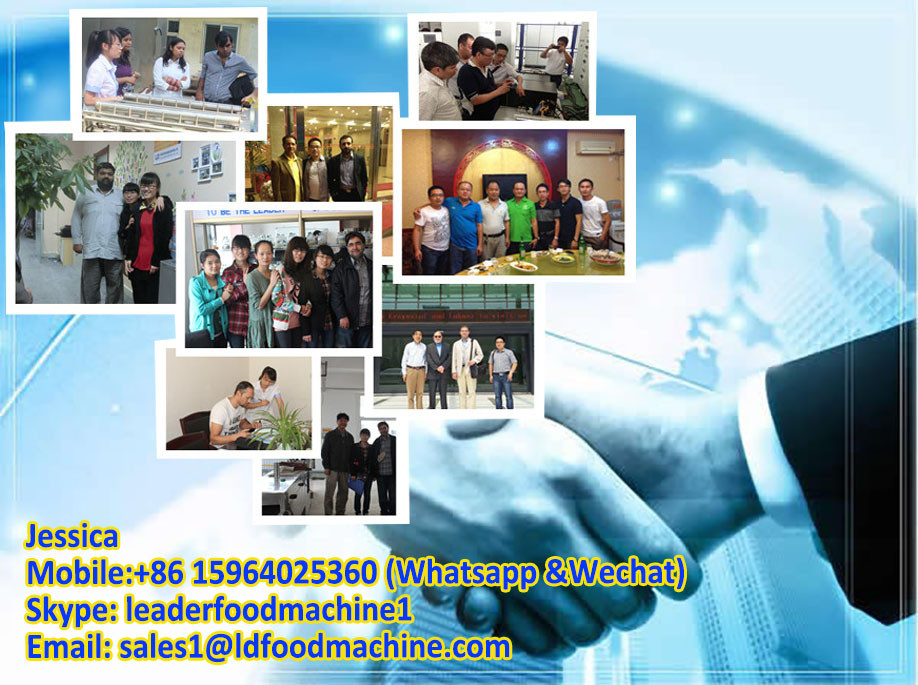
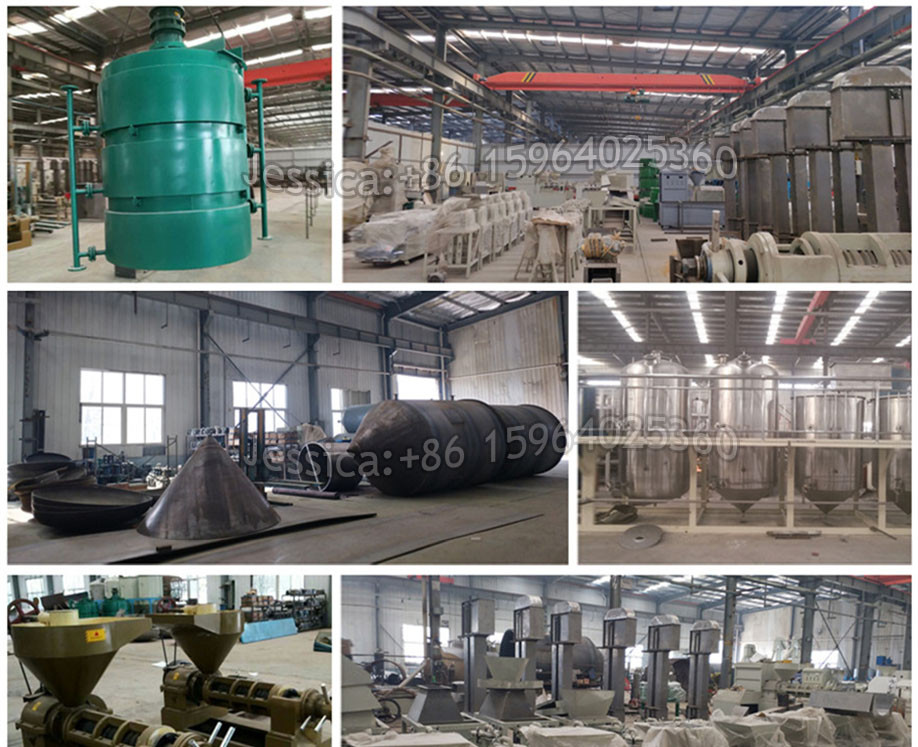

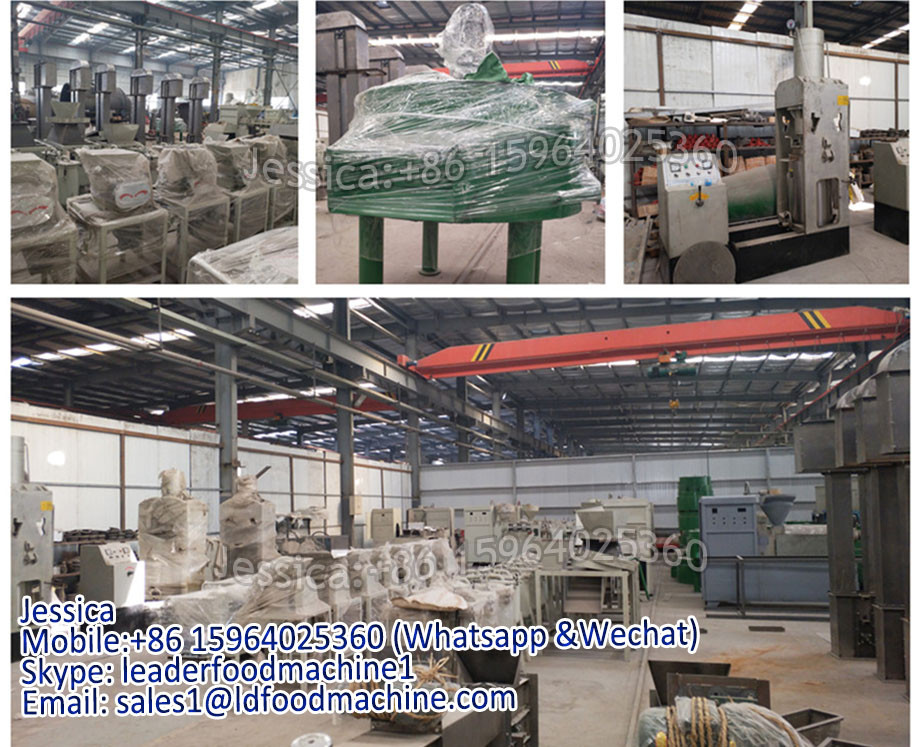
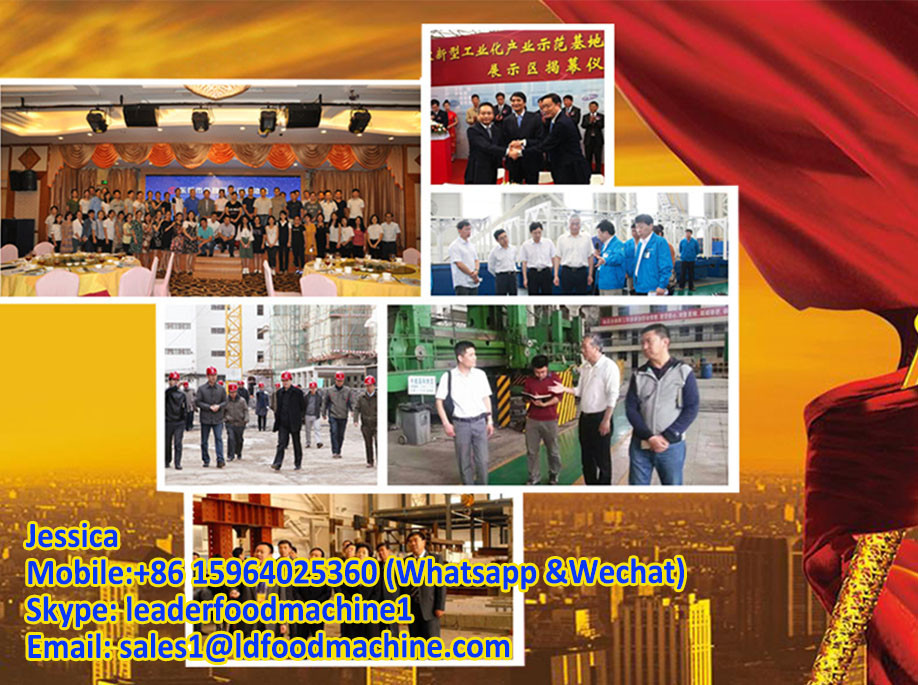
FEATURES OF EXTRACTOR:
1. Adopt stainless steel fixed grid plate and increase the horizontal grid plates, which can prevent
the strong miscella from flowing back to the blanking case, so as to ensure good extraction effect;
2. The rotocel extractor is driven by rack, with unique rotor of balanced design, low rotating
speed, low power, smooth operation, no noise and quite low maintenance cost;
3. The feeding system can adjust the rotating speed of airlock and main engine according to the
feeding quantity and maintain a certain material level, which is beneficial to the micro negative
pressure inside the extractor and reduce the solvent leakage.;
4. The advanced miscella circulation process is designed to reduce the fresh solvent inputs,
reduce the residual oil in meal, improve the miscella concentration and save energy by reducing
the evaporation capacity;
5. The high material layer of the extractor helps to form immersion extraction, reduce the meal
quality in miscella, improve the quality of crude oil and reduce the evaporation system scaling;
6. Specially suitable for the extraction of various pre-pressed meals.
WET MEAL DESOLVENTIZING PROCESS:
Desolventizer toaster advantages:
a) Passivate and damage the anti-nutritional components such as the urea enLDme and trypsin in the meal, and improve meal
value in use.
b) Control the protein denaturation degree in the meal , and improve the NSI index effectively.
c) It can better regulate the color, flavor and taste of the meal.
d) It can reduce residual solvent in the meal and regulate the meal moisture, so as to guarantee
the minimum solvent consumption and safe use of the meal.
NEGATIVE PRESSURE EVAPORATION PROCESS:
The liquid from the extractor is the miscella containing grease and oil, which can be separated
out according their different vaporization temperatures.
Our company mainly uses vacuum evaporation technology, and it can reduce solvent leakage
and consumption. The separated solvent vapour is cooled and recycled back to the extractor for
reuse, which can improve the solvent efficiency.
SOLVENT CONDENSATION & RECOVERY PROCESS:
Solvent condensation system combines with evaporation system closely, and evaporative
condenser and steam stripping condenser all work under negative pressure.
Non-condensable gas enters the energy saver from the shell of the first evaporator. In energy
saver, noncondensable gas exchanges heat with condensate from the evaporative condenser.
Finally, the condensate temperature discharged from energy saver is increased, and the solvent
separated from water goes to solvent holding tank.
The high temperature makes it unnecessary to be reheated for the recycling, so as to save energy.
Noncondensable gas from energy saver enters desolventizing condenser, in which a great deal of
gas is condensed, and the tail gas is discharged into the final condenser.
The solvent gas from the extractor enters extraction condenser, and the noncondensable tail gas
enters the final condenser.
For the free gas in final condenser, diversion box, holding tank, underground solvent library and
miscella tank, cool them with low temperatured cold water to recycle most of solvent gas. The
tail gas with little solvent goes to paraffin recovery process.
WHAT CERTIFICATES DO WE HAVE?
Still have questions?
What should you do??
Do not worry!
Jessica is always here!!
Just knock me!!!