5-150TPD machine to make peanut oil
Contact Me
Name: Alice
Phone: 0086 18736001536
Company Information
Our company is a manufacturer of all kinds of oil production line equipment; Our company was established in 1989. We have a big plant and have rich experience in this field. We have exported to many countries like Egypt, Chile, Argentina, Ethiopia, Zambia, Nigeria, Russia and Turkey ect.

1.Absorbing the world’s leading core extraction technology, design and develop a process which is efficient, economical and reliable. Adopting box-chained loop type extractor can effectively achieve low residual oil, low solvent consumption and low failure rate of equipment. Thus, customers will have little cost and investment, and profit maximization will be achieved.
2.Full automatic computer control system is adopted in extracting process, adjust automatically and operate stably.
3.Negative pressure technology is adopted in condensate system. Using the secondary steam which comes from the DTDC as the heat source of first evaporation, thus can maximum save the energy consumption.
4.Stainless steel heat exchange tubes and multi-stage baffling make the condenser have a high heat transfer efficiency, also the water consumption is low.
5.Composed of pre-extraction, extraction and draining sections. There is material turnover in the process of extraction to make the extraction uniform and thorough. Special self-cell solvent spraying ensures the best effect during extraction.
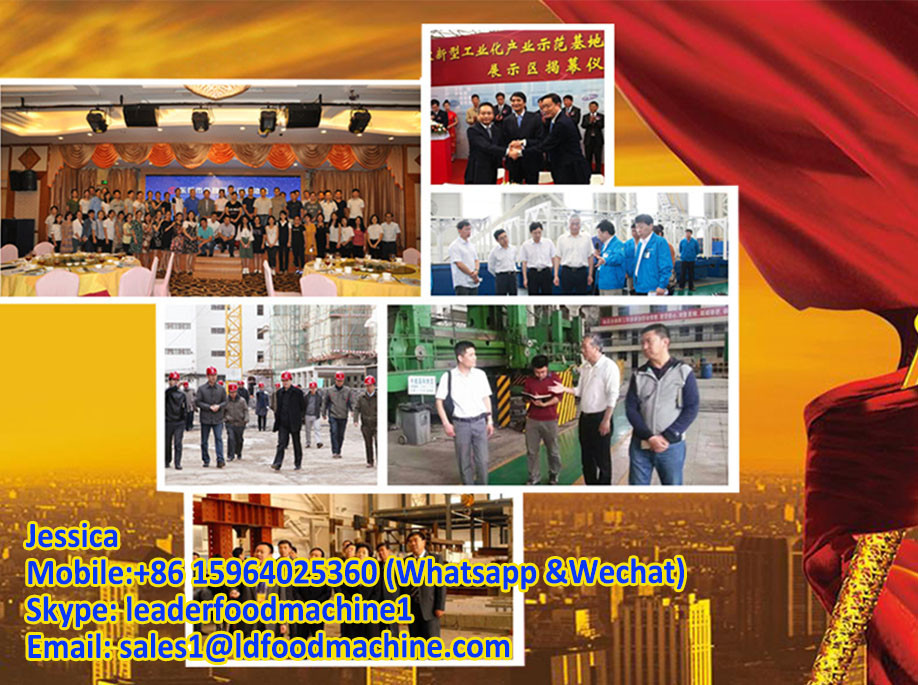
Process details:
1. Extraction process
The pre-pressed cake or flake, firstly enters into the seal auger to avoid the solvent gas escaping. Then material enter into the box-chained loop type extractor and counter-currenting with the solvent, the grease is extracted, and miscella concentration increases from 2% to more than 25%. Then miscella is discharged from extractor, and into miscella filter for filtration. After separating fines, miscella enter into the oil tank, then pump into evaporation system. And the leached meal finally drops in DTDC through buried scraper plate.
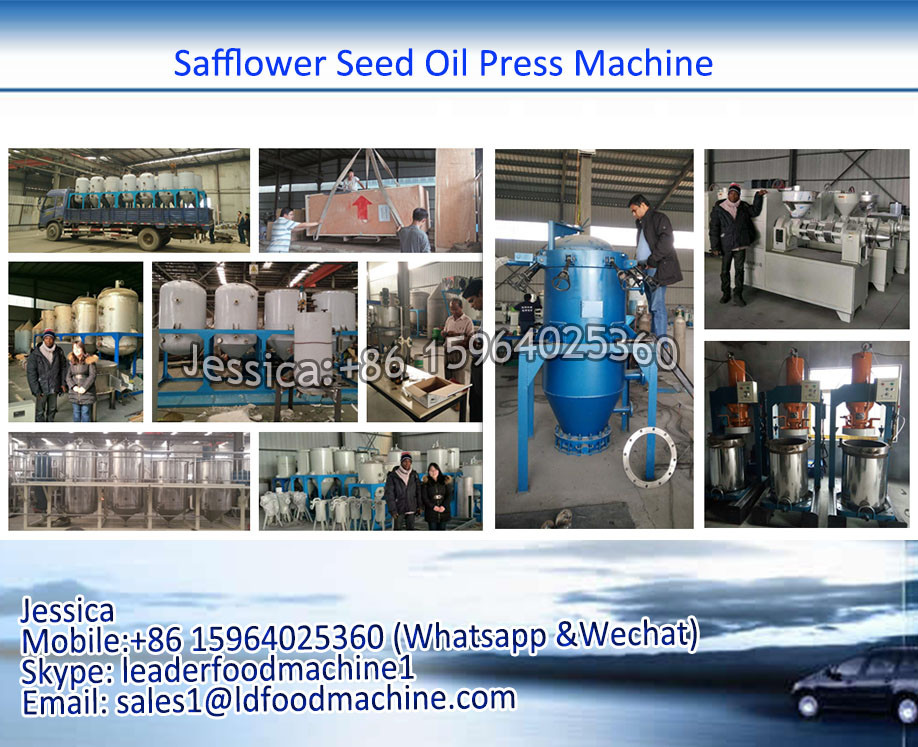
2. Evaporation process
Using the secondary steam desolventized from DTC desolventizer and produced by steam-jet pump to heat and evaporate micella in the first long-tube evaporator. Export temperature reaches to 58-62℃ and concentration reaches to more than 65%. Then, micella enters into the second long-tube evaporator in which the temperature is heated to 105-110℃ by indirect steam and the concentration reaches to more than 95%. Then miscella enters into stripper in which residual solvent in oil will be removed, the export temperature reaches to about 105℃ and the general volatile of the extracted crude oil is less than 0.30%.
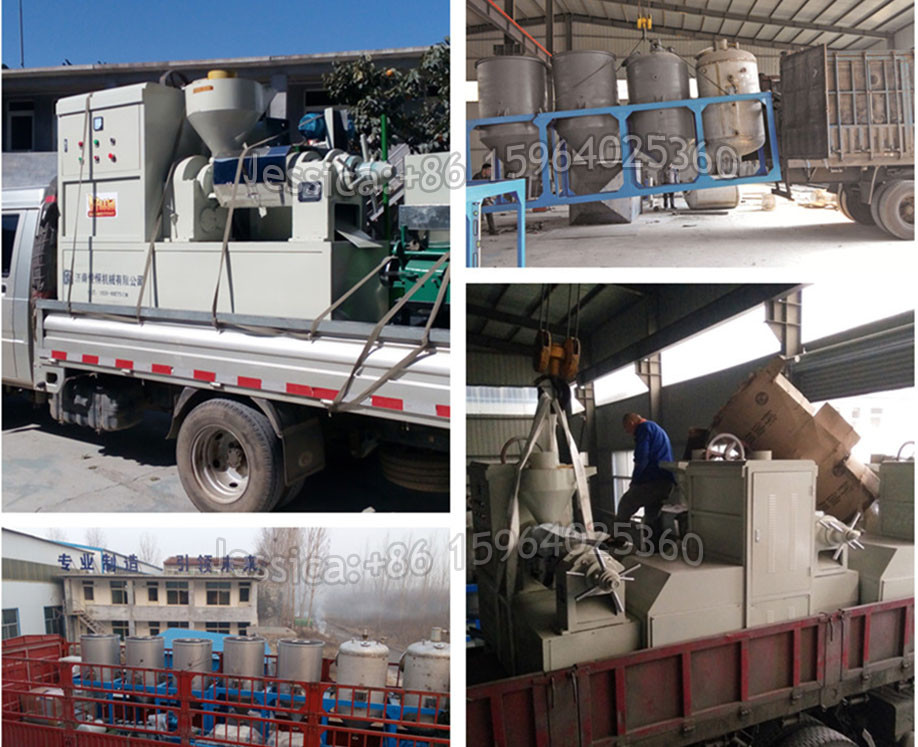
3.Desolventizing process
Wet meals discharged from the bottom of extractor enter the top of DTDC and land on the predesolventizing trayers where they are heated by the indirect steam, thus, some solvent in meal is evaporated and meal temperature is risen; Predesolventized meals land on predesolventizing trayers where they use the second steam in desolventizing trayers to predesolventize solvent from meal, then, meals enter desolventizing layers in which direct steam is injected. Direct steam is sprayed into the meals through the bottom holes, and distill the solvent from meal by using steam in order to remove all solvent; Desolventized meals land on the following drying and cooling layer to dry and cool meals,cooled meals land on meal scraper blade from automatic material controlling gate on the bottom of cooling layer, and then they are entered into meal storehouse.
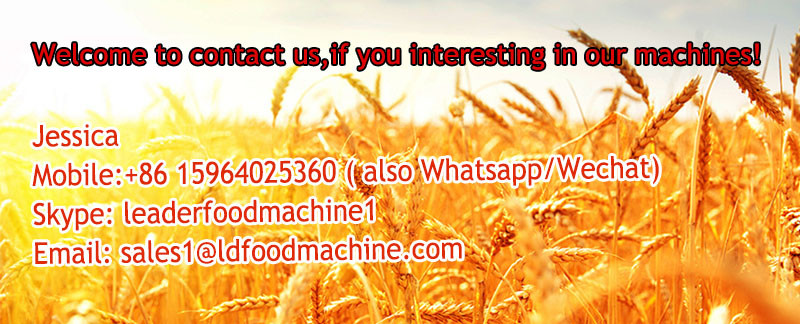
4. Condensation recovery
DTDC is equiped with a separate condenser, 1st and 2nd evaporation share one condenser. Low and high temperature of solvent gas both from 1st and 2nd evaporation enter into the condenser after its neutralization, which greatly reduces the load of condenser and improves the efficiency of condensing. Stripping and analyzing share one condenser, the non-condensable gases from extractor and other condensers enter into the vent gas recovery system through the final condenser.
In the recycling system, the cold paraffin will absorb the solvent gas and the final nonsolvent gas will be discharged through fire resistance valve.Paraffin absorbed the solvent gas can be also called rich oil, after heating by oil-oil heat exchanger and steam, the rich oil will enter into desorber for desorption, and into condenser after changing solvent into gas, the final cooled paraffin can be recycled.
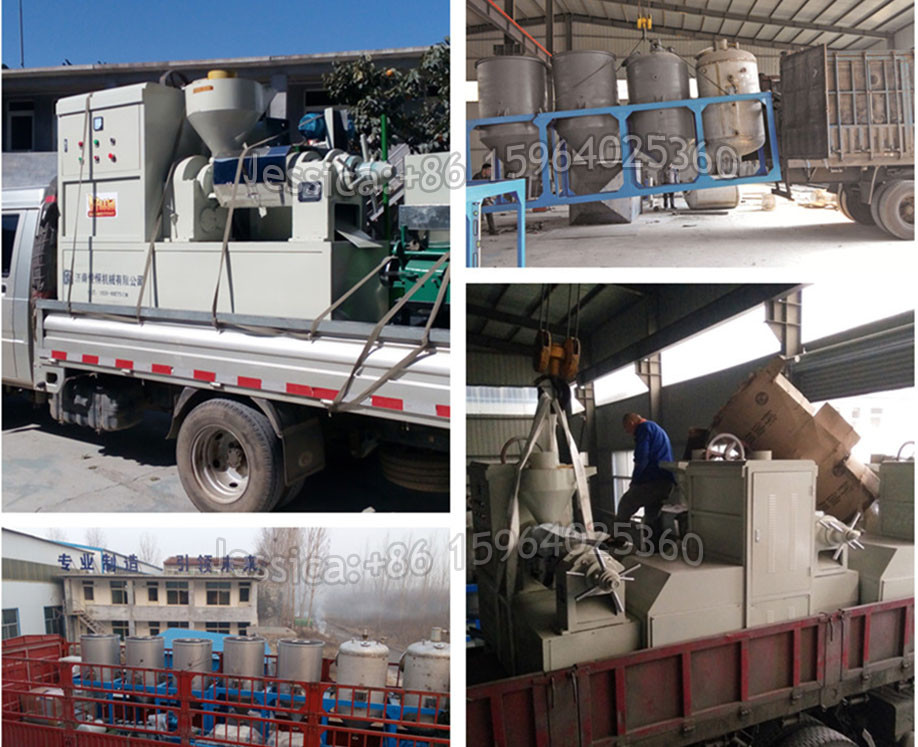
Crude oil refining pot
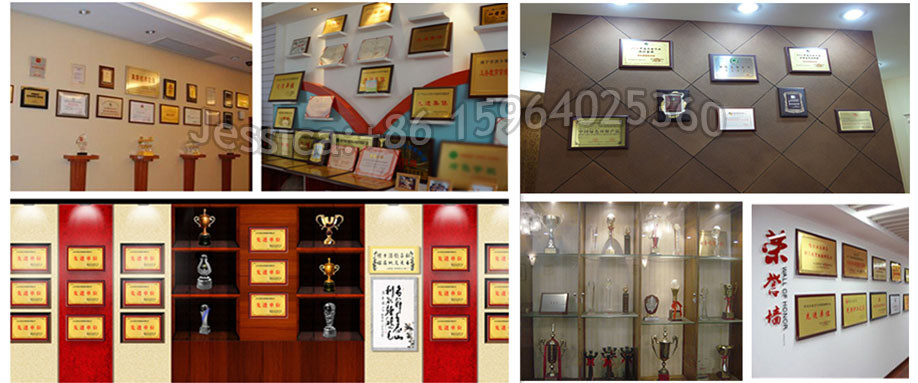
Oil deodorizing tower
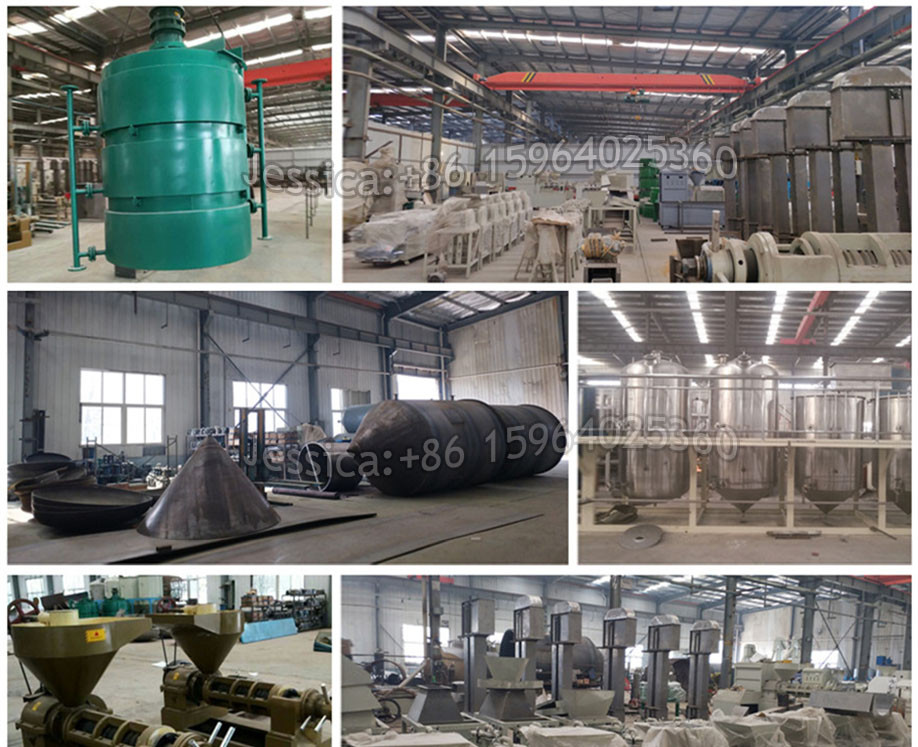
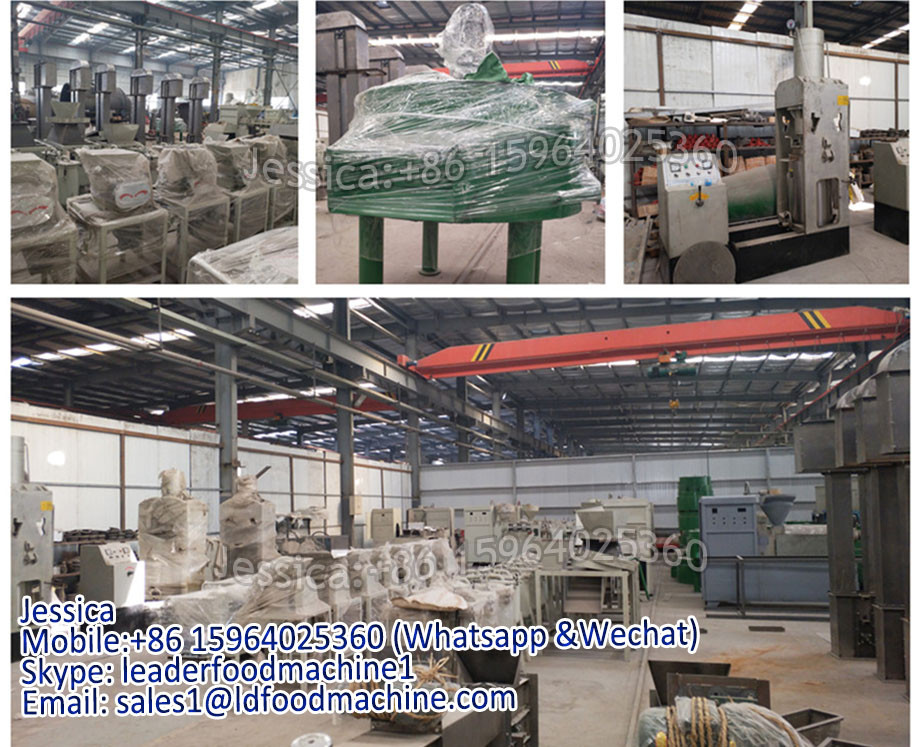
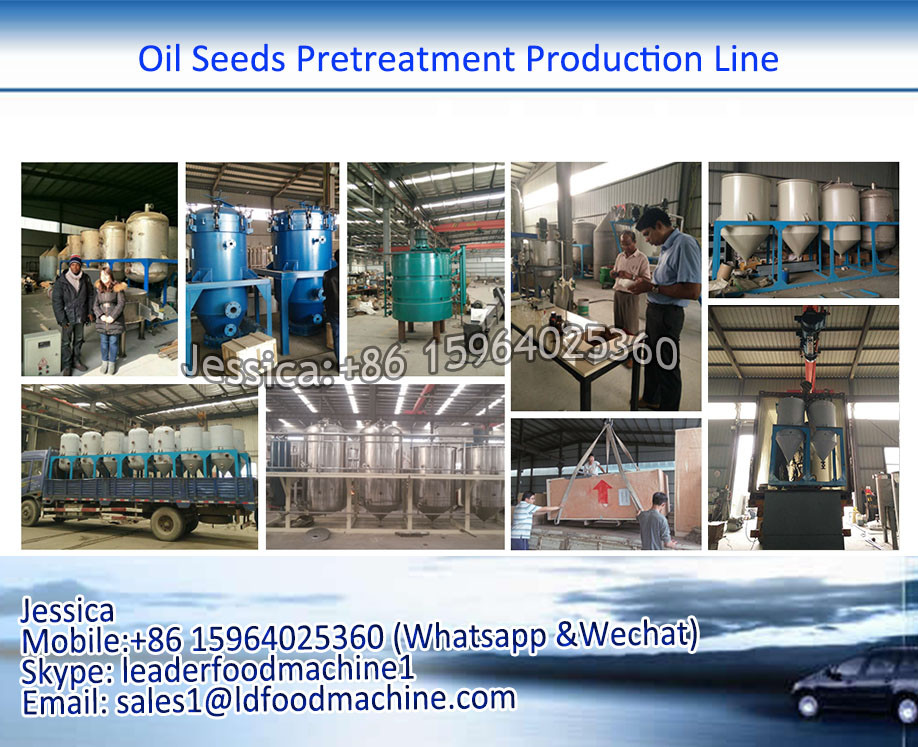