Introduction
Pre-press leaching and oil refining equipment is suitable for the normal pressure/micropressure/water decoction/warm maceration/hot reflux forced circulation/permeation extraction & concentration,organic solvent recovery concentration and other processes in Chinese traditional medicine, health products, biological, pharmaceutical, cosmetic and food industries.This is the ideal equipment for Shandong Leader Machinery Co.,ltd., research institutes,research and development departments and laboratories of enterprises and institutions,and many varieties,small batch production of pharmaceutical plant.
Pre-press leaching and oil refining equipment
Product Description
Main Technology
1,Pretreatment and Pre-pressing technology.
2,Solvent Extraction Technology.
3,Edible oil Refining Technology.
4,Dewaxing and Degreasing Technology.
5,Soybean protein concentrated and protein isolates Technology.
6,Peanut oil cold pressing and superfine fragrant peanut oil Technology.
7,Palm fruit pressing Technology.
8,Palm oil fractionation Technology.
Available oil crops
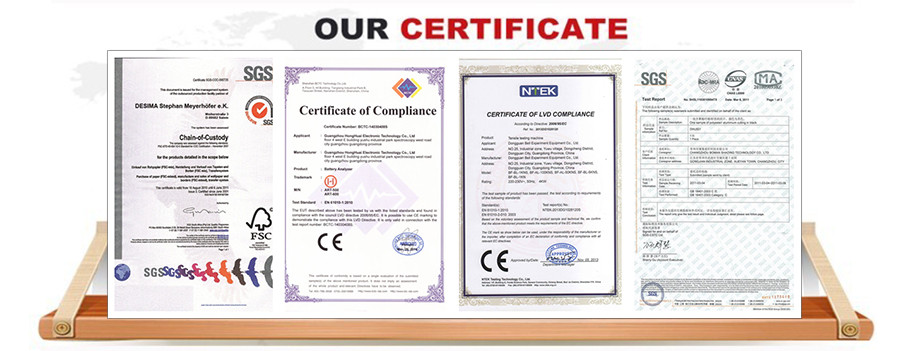
Pretreatment process feature:
1) Different combinations of process can process various oil plants in one workshop.
2) Use special intensified pretreatment technology for aroma peanut oil to make it more aroma.
3) Adopt advanced and reliable shelling technology to meet higher requirements for protein content in meal.
4) Extrusion treatment is used for raw materials with hard extraction, large-sized powder, and large capacity, which can reduce residual oil and solvent consumption, and increase the capacity by 50-80%.
5) The new technology of shelling and low-temperature treatment can ensure high protein and least denaturation.
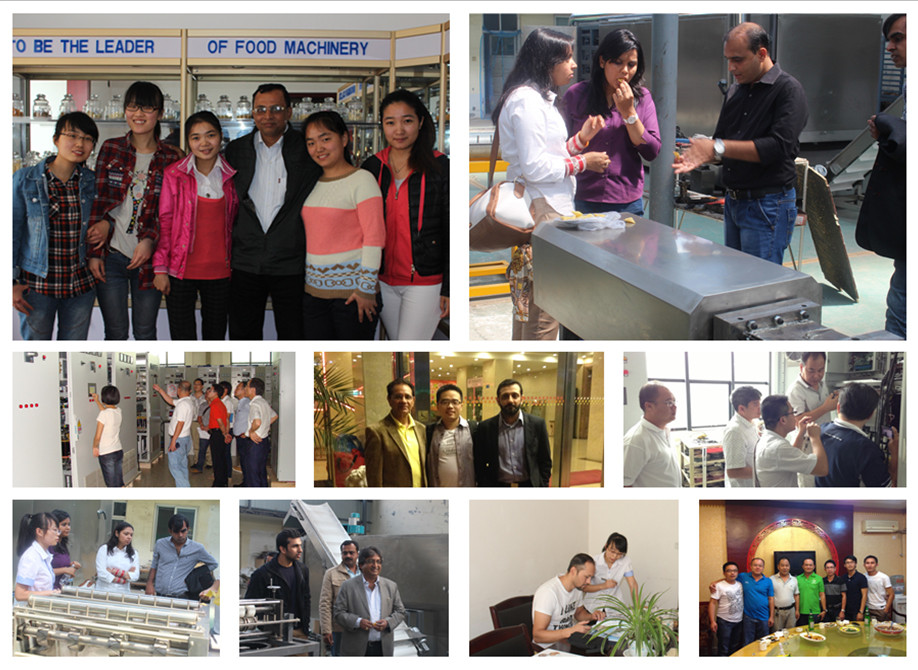
Flaking machine
Solvent Extraction Flow chart for soybean oil
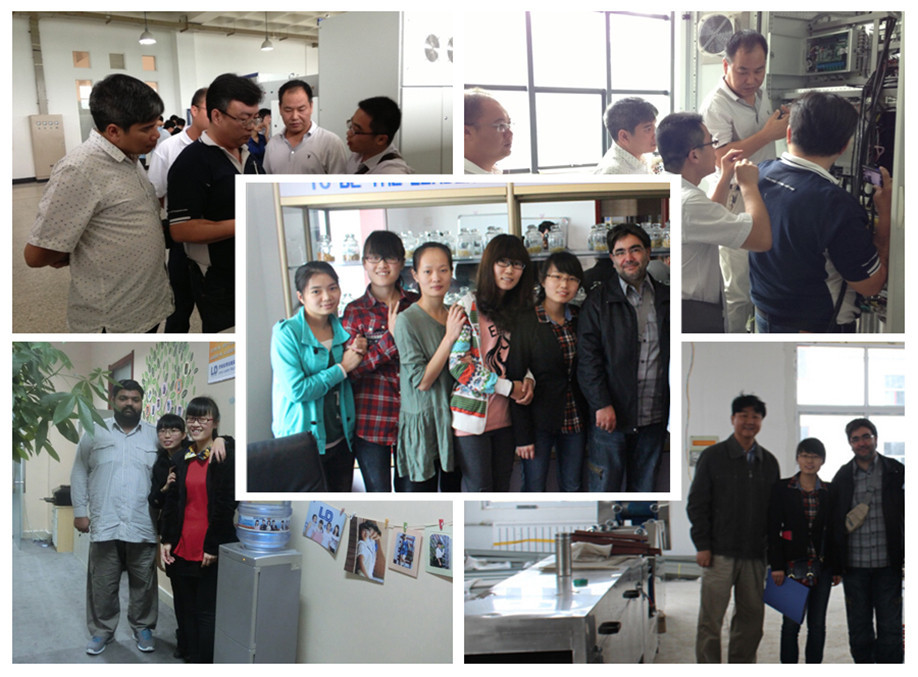
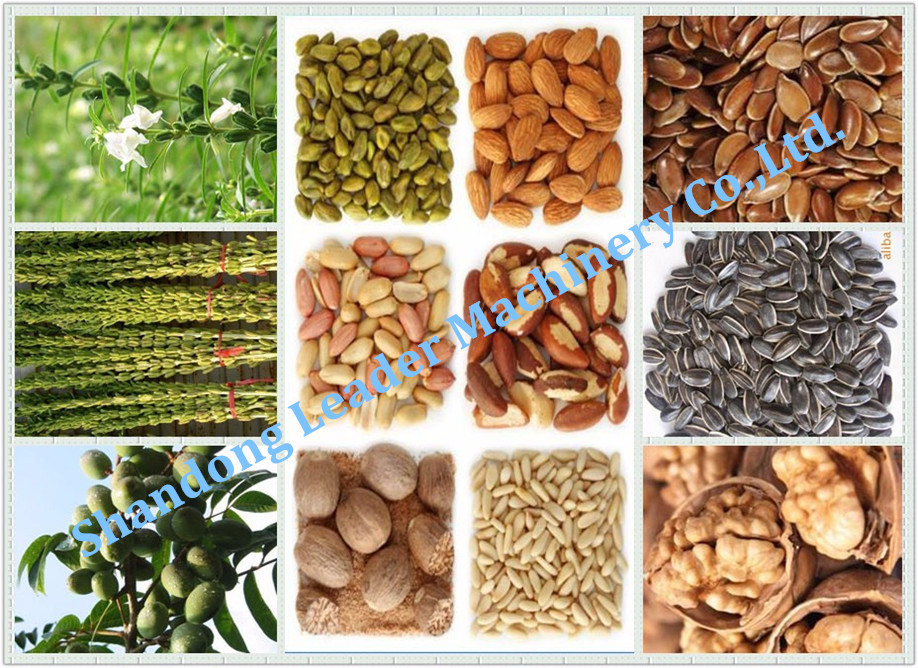
Rotocel Extractor
1. Adopt stainless steel fixed grid plate and increase the horizontal grid plates, which can prevent the strong miscella from flowing back to the blanking case, so as to ensure good extraction effect;
2. The rotocel extractor is driven by rack, with unique rotor of balanced design, low rotating speed, low power, smooth operation, no noise and quite low maintenance cost;
3. The feeding system can adjust the rotating speed of airlock and main engine according to the feeding quantity and maintain a certain material level, which is beneficial to the micro negative pressure inside the extractor and reduce the solvent leakage.
4. The advanced miscella circulation process is designed to reduce the fresh solvent inputs, reduce the residual oil in meal, improve the miscella concentration and save energy by reducing the evaporation capacity.
5. The high material layer of the extractor helps to form immersion extraction, reduce the meal quality in miscella, improve the quality of crude oil and reduce the evaporation system scaling.
6. Specially suitable for the extraction of various pre-pressed meals.
Desolventizer(LD)
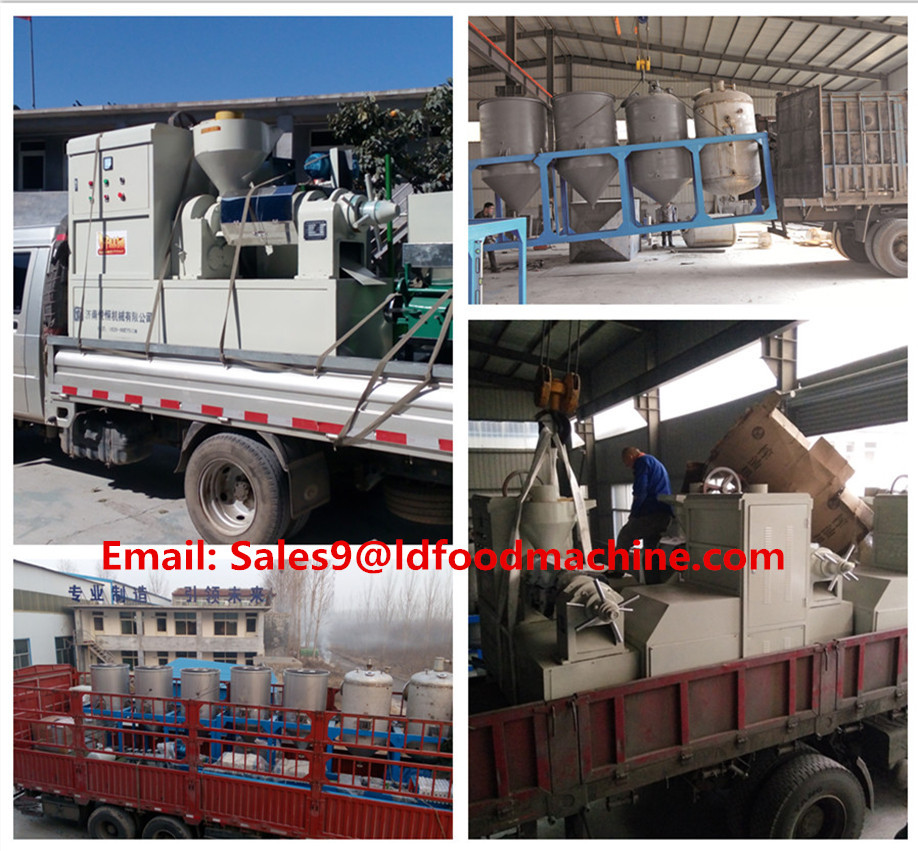
Solvent condensation & recovery
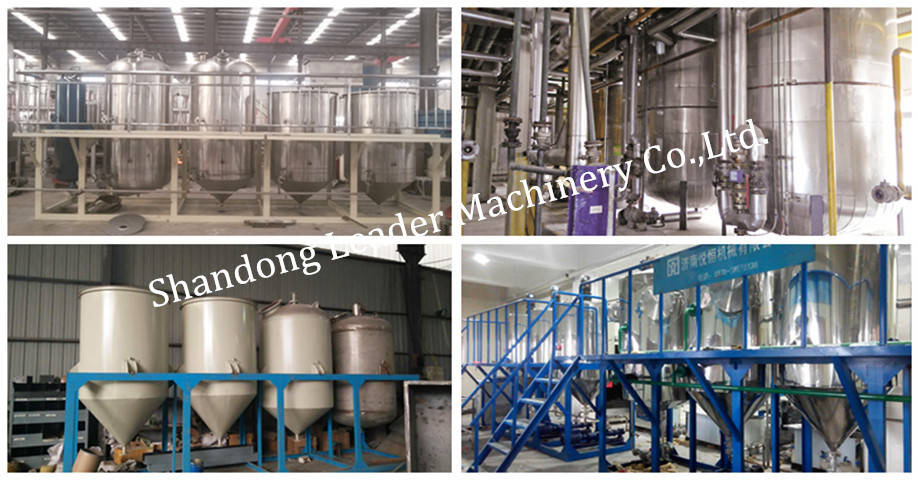
Main Parameters
Residual oil in meal |
â¤1% (Peanut) |
Solvent consumption |
â¤3Kg/T(6#solvent oil) |
Crude oil moisture and volatile matter |
⤠0.30% |
Power consumption |
⤠15KWh/T |
Steam consumption |
â¤280Kg/T (0.8MPa) |
Finished meal moisture |
⤠10-13% (adjustable) |
Residual solvent in finished meal |
⤠300PPM (qualified detonated experiment |
The advantage of LD desolventizer1, Passivate and destruct the anti-nutrition in the meal, such as the urease and the trypsin,improve the use value of the meal.2, Control the protein denaturation degree of the meal, effectively improve the mealâs NSI index3, To adjust the color, flavor and granularity of the meal.4, To reduce the residual solvent in the meal, adjust the moisture of the meal, to ensure the lowest solvent consumption and safe use of meal in production.
Refining flow chart for soybean oil
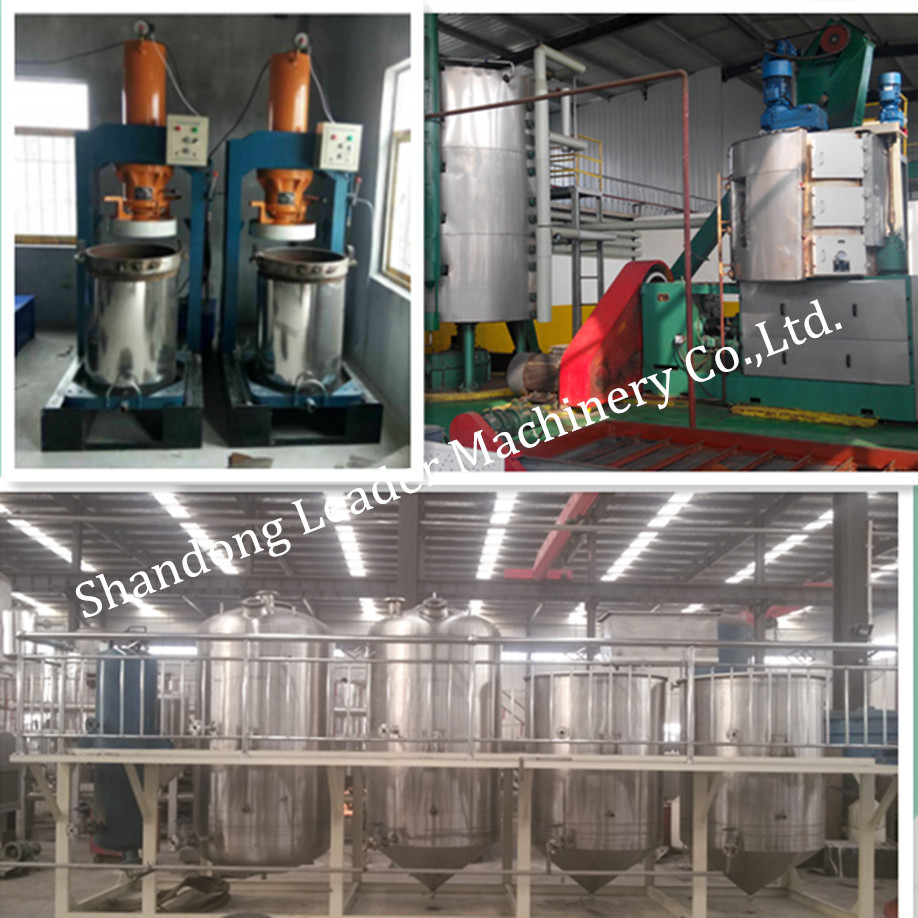
Main Paramaters
Soft water consumption |
⤠160Kg/H |
Steam consumption |
⤠300Kg/T oil |
Bleaching earth |
1-3Kg/T oil |
Power consumption |
⤠22KWH/T oil |
Fuel consumption |
10-20Kg/T oil |
Oil content in waste white clay |
⤠23% |
Phosphoric consumption |
0.5-1Kg/T oil |
1.Deacidification
Sodium hydroxide antagonize free fatty acids,and subside phospholipids,to remove the insoluble impurities,then after the separation of soapstock, neutral oil was washed in soft water,last drying in vacuum.
2.Bleaching
Used to remove off pigments, bleaching oils and grease dehydrate
3.Deodorization
Using high temperature and high vacuum steam stripping method deodorization temperature commonly 180, vacuum degree 9.3 104 Pa can achieve ideal results
4.Dewaxing
Dewaxing can ensure the colour of the oil to be clear bright at room temperature and frozen temperature. to reduce the oil in the wax content to 10 parts per million to get crystal clear oil.
Process characteristics of 3T/D edible oil refining equipment.
Process description:
The whole process of intermittent refining:
Oil inletâheating upâdeacidificationâdealkalizingâwashing 2-3 timesâdry dehydration. The total time is about 24 hours.
According to the difference of alkali thickness and oil temperature, the process of dealkalizing is divided into two types, one is low temperature with thick alkali (its initial temperature is 20 ~ 30 â, alkali thickness is 20 ~ 30 Be) and another one is high temperature with light alkali (its initial temperature is 75 â, alkali thickness is 10 to 16 Be). The former is generally applied and the latter is mainly used for crude oil which has low acid value, light clour and lustre, and less impurity.
I. Low temperature with thick alkali:
Adjust the oil temperature to 20~30â, then put in 20~30Be alkali liquor in 5~10 minutes, and stir it about 20~60 minutes on condition of 60r/m. Increasing the temperature slowly when notice the separate of neatsoap after reacted, 1â per minute, when it reach 60â, stop stiring, keep still and make soap feet settlement, it will takes nearly 6~8 hours, then let out the soapstock.
â ¡. High temperature light alkali operation:
Firstly,determine the alkali thickness in accordance with the alkali value of crude oil(according to the table below), account the alkali and water added in, when the alkali value is under 5, for each unit acid value, the total water added into per ton oil is 23 kg. When the alkali value is over 5, no more than 12% of the oil heavy, the exceeded alkali is only 0.005~0.002%.
Crude oil alkali value |
|
3~5 |
5~7 |
7~10 |
>10 |
Alkali thickness Be |
10 |
11 |
12 |
14 |
16 |
When operating, first mix the crude oil, heat the temperature to be 70 ~ 75 â diluted saline or phosphoric acid (concentration 90%) , when particles appear, add alkali, then continue to stir for 40 ~ 50 minutes and heat up to be 90 ~ 95 â until soap obviously separated, and put into nigre after 2 ~ 3 hours' static.
â ¢. Washing:
After releasing the nigre, grease heated up to boom 90â, then add in the hot water for washing, stirring. Water temperature should be about 5 ~ 10 â higher than the oil temperature, for low water temperature tends to emulsification. After adding the water, continue to stir for 5 minutes, then rest 4 hours for precipitation, and release the soap water, wash 2 ~ 3 times depending on the oil quality and decide. Washed oil slowly heated up to 105â, stirred dehydration for 1 hour, washed oil can also direct inhaled decoloring pot and vacuum drying 30 minutes.
Method of operate for descoloring
1 start the vacuum pump,vacuum degree â¥700mmHg
First, after washing of alkali refining inhaled decoloring pot, stirring, at the same time warming up to 90 â, and stir another 30 minutes, decrease moisture below 0.1%, then inhale a few decoloring agents "white earth, activated carbon >, the quantity depends on the oil color, generally, oil amount 2 ~ 4%, stirring 30 minutes, cooled to 70 â, use compressed air pressure to filter oil machines to separate the white earth and oil, then get decoloring oil.
Method of operate for deodorizating
l By vacuum pump oil bleaching inhaled deodorization pot, up to 755 mmHg in vacuum degree , begin distillation and deodorization timing;
l Deodorizating time : 4 Hours
l Deodorization temperature: 240â/755mmHg~260â/759mmHg
l Deodorization vacuum degree: above 755mmHg
l There is steam distillation during the whole timing process.
l After deodorization, shut off the direct steam in vacuum condition , close conduction oil,open the valve for cooling water.,until the oil temperature nearly 40~80 â,shut off the vacuum pump valve,make test of the oil sample,if it is passed inspection,packing and finish all the manufacturing of edible oil.
Characteristics
l Both short mixed and long mixed process are adapted in washing sector, which ensures washing effectiveness.
l Equipped with vertical leaf filter to remove used bentonite from the oil, operating conveniently and continuously, low laboring tense, keeps environment well, keeps oil residence in deposable bleaching earth in low level.
l Due to accurate stirring method, decreased the maximum distance between the oil of cooling facet so as to ensure the same temperature of crystal with same quality. Better guaranteed that in the process of crystallization, crystal will not cluster in a intense area.
l Flexible system, cooling curve can be easily altered by changing water temperature, thus the kinds of products can be changed easily.
The main economic technical parameters:
Capacity T/D |
3T/D |
Steam consumption |
900KG/T oil |
Electric consumption: |
28Kwh/T oil |
Water(soften water) |
150Kg/T oil |
Phosphoric acid |
2~3 kg/T oil |
Alkali |
Acid valuex1-3kg/T oil |
Circulating water cooling water yield |
150M3/H |
Bleaching earth consumption |
3-5Kg/toil |
Waste bleaching earth oil content |
|
Refining losses |
Acid valuex1.2(chemical refining) |
acid valuex |
0.6(physics refining) |
Bleaching losses |
The quantity of bleaching earthÃ0.25% |
Deodorization loss consumption |
â¤0.5% |
Refining rate |
1-refining consumption % |
Company Information
We specialize in manufacturing oil making machine and equipment. Established in 1978. With more than 30 years experiences in this field, We have exported our equipments to many countries like Egypt, Chile, Argentina, Ethiopia, Zambia, Nigeria, Russia and Turkey etc.
Approvals
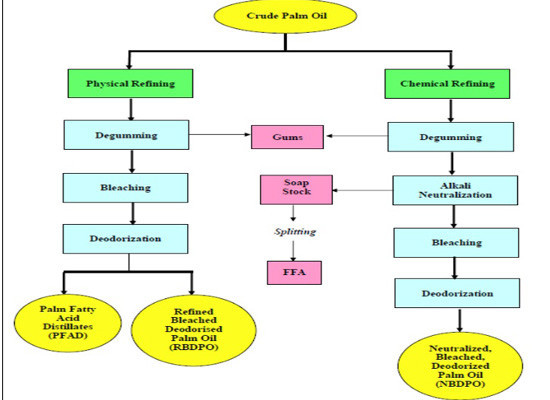
Laboratory
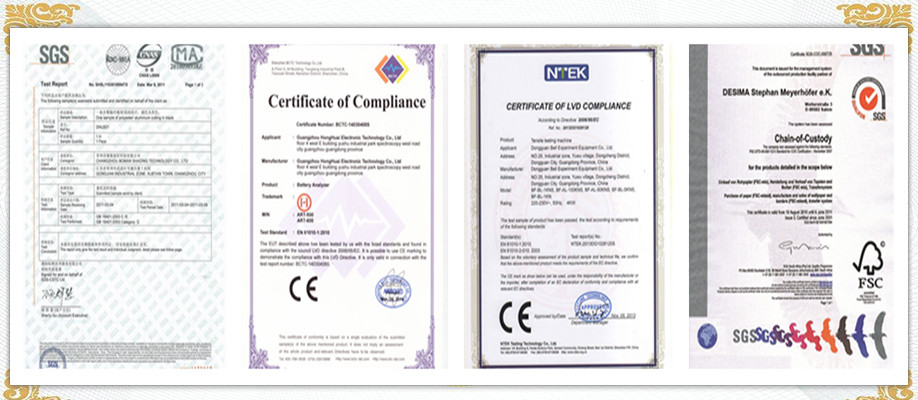
Workshop
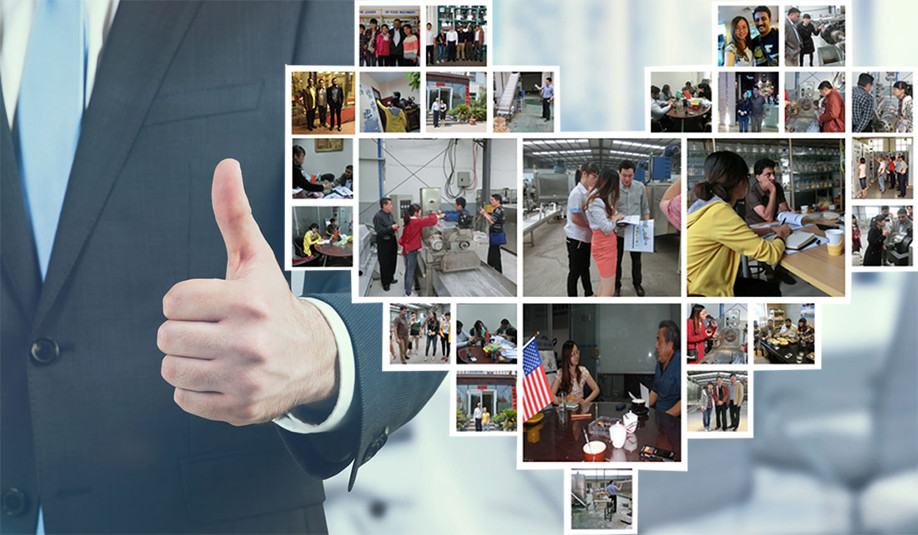
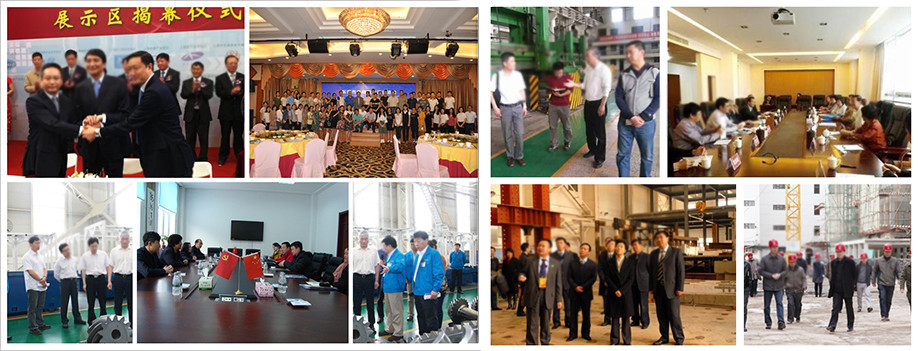
Pre-sale
System evaluation: 1)Project basic situation
Solution: 1)The investment budget. 2)Feasibility, rationality
Product selection: 1)Factory inspection. 2)Site measurement. 3)Technical discussion. 4)Supply professional drawing and lists.
Win--win coopration: 1)Sign the contract. 2) Establish mutual benefit, strategic cooprative partnership.
In-sale
Design evaluation:1) Detailed technical assessment, arrangement. 2)Design of process and equipment layout.
Procurement: Strictly inspection, optimized selection.
Installation: 1)Quality and quantity guaranteed. 2)Completion of hand over.
Acceptance:1)Acceptance test. 2)Accepted deliverable
Technical training: 1)On-site installation and products training. 2) Operation skills training. 3) Maintenance training. 4) Centralized technical training
After-sale
Technical service: Long time technical service
Accessories supplying: Supplying spare parts with cost price.
Feel free contact me to get more information
Pre-press leaching and oil refining equipment Features
v High efficiency: On the basis of original single vertebral and oblique vertebral structure,this device optimizes the product structure and integrates the concentration equipment to have the function of extraction,concentrate and organic solvent recovery.This device can do the hot reflux recycle extraction and concentrate,normal extracion and concentrate etc,simplifying the operation procedures,make the extraction,filtration,concentrate,condensation and other production processes completed in one step,greatly saved the material and extraction time.Working efficiency has improved by 20~35% compared with the general extraction machine.
AAA1
Pre-press leaching and oil refining equipmentv High conversion rate: During the extraction process, the hot solvent (water or alcohol) is added to the material continuously,the solvent from top to bottom pass through the material dissolved the active ingredient,so that the active ingredients in the material liquid is increased by more than 1 times than the average extraction.
AAA2
If you have any demand about microwave drying equipment and edible oil refining equipment, pls feel free contact us any time.
LD Miss Candy
Skype: leaderfoodmachine9
Mobile: +86 18363700691 (Also WhatsApp & Wechat)
Email: [email protected]