Specifications
1 suitable for large scale drying.2 high efficient dryer.
3 widely used in various industries
Rotary drum dryer/drting equipment
Descriptions:
Mostly the machine is used in per burning of rigid magnet oxygen Pulverized fodder; it is also suitable for the cement, metallurgy and Chemical industry. It is made up of main kiln body and supporting Drive set cooling pipe and supporting drive set, fuel system, electricity Control secondary air set, exhaust dust set and warm-up kiln body etc. The machine has function like: give an alarm for over temperature, give an alarm for over loading, auto control for working temperature, oxygen atmosphere is adjustable in the kiln etc.
Principle:
When the damp raw material is fed from one terminal, it is turned over through blades that are distributed inside the cylinder and will be distributed uniformly in the drier and contact fully with the countercurrent hot air. In this way, the process of heat conduction is increased. During the period of dry, under the effect of incine blades and hot air stream, raw material can be moved to the star section of drier and discharged from disharged form discharging valve.
Applications:
1 It is suitable for drying the following raw materials. They are granules with heavy specific gravity in chenmical industry, mine industry, metallurgy industry such as ore, slag, coal, metallic powder, phosphorus fertilizer, ammonia sulfate.
2 Moreover for raw materials that are granules with special requirements, such as HP vesicant, less, light calcium carbonate, active white earth, magnetic powderm, graphite, lag of medicine
3 Raw materials that need low temperature and in batch continuously.
Features:
1 High in the etent of mechanization and strong in production capacity.
2 The resistance for fluid passing through the cylinder is small. The consumption of power and energy is low.
3 It has strong adaptability to the properties of raw material. The operation is stable. The cost of operation is cheap.
4 The uniformity of dried substance is good.
Form | Direct heating down-stream | Direct heating reverse-flow | Compound heating | |||
Kinds of raw material | Ore | HP Vesicant | Ore residue of blast furnace | Ammonium sulphate | Phosphorus fertilizer | coal |
Amount to be treated kg/h | 1000 | 466 | 15000 | 20000 | 12000 | 5000 |
Primary moisture % | 30 | 13 | 6 | 1.5 | 5 | 6.5 |
Final moisture % | 15 | 0.3 | 1 | 0.1 | 0.1 | 0.1 |
Average diameter mm | 6.5 | 0.05 | 4.7 | 0.5-0.7 | 0.5 | 5 |
Specific gravity of raw material kg/m2 | 770 | 800 | 1890 | 1100 | 1500 | 750 |
Amount of hot air m3/kg | 39000 | 5400 | 10750 | 9800 | 6500 | 16000 |
Temperature of air at inlet in °C | 600 | 165 | 500 | 180 | 650 | 570 |
Temperature of product at outlet°C | 42 | 100 | 70 | 80 | 75 | |
Heating way | Gas | Steam,electric heating | Heavy oil | Coal fuel hot air furnace | Heavy oil | Heavy oil |
Loading coefficient | 6.3 | 7 | 7.5 | 7.8 | 18 | |
Revolution rpm | 4 | 4 | 3.5 | 3 | 4 | 2 |
Gradient m/m | 0.04 | 0.005 | 0.03 | 0.05 | 0.05 | 0.043 |
Quantity of stirring-up rake | 12 | 24 | 12 | 22 | Outer of inner cylinder 8 ,Inner of outer cylinder 16 |
Outer of inner cylinder 6 ,Inner of outer cylinder 12 |
Diameter of dryer m | 2.0 | 1.5 | 2 | 2.3 | Outer of inner cylinder 2, Inner of outer cylinder 0.84 |
Outer of inner cylinder 2.4, Inner of outer cylinder 0.95 |
Length of dryer m | 20 | 12 | 17 | 15 | 10 | 16 |
Driving power kw | 22 | 7.5 | 15 | 11 | 11 | 15 |
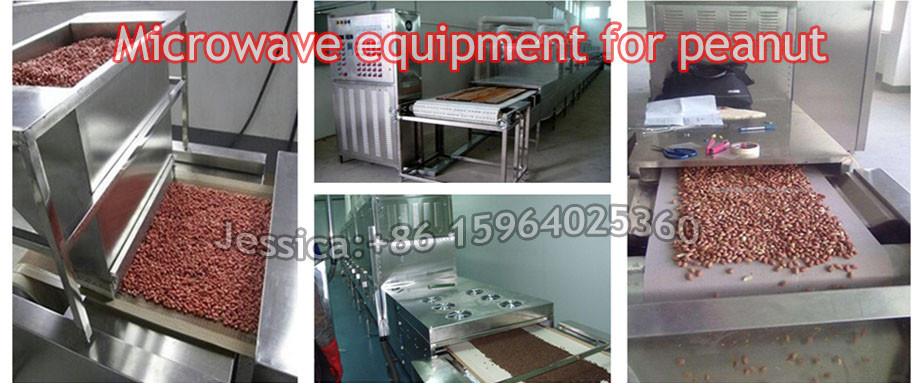
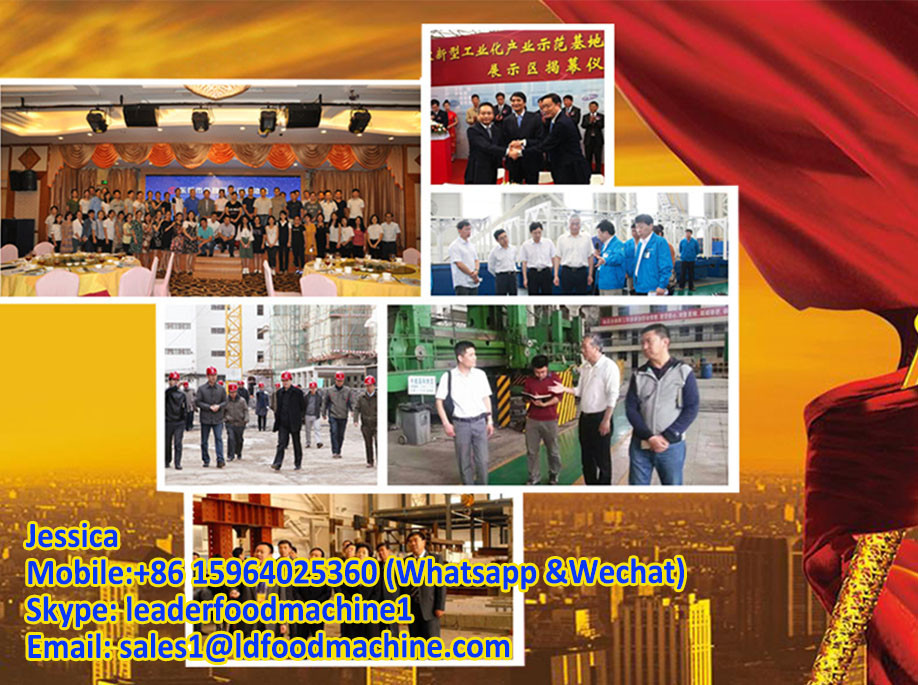
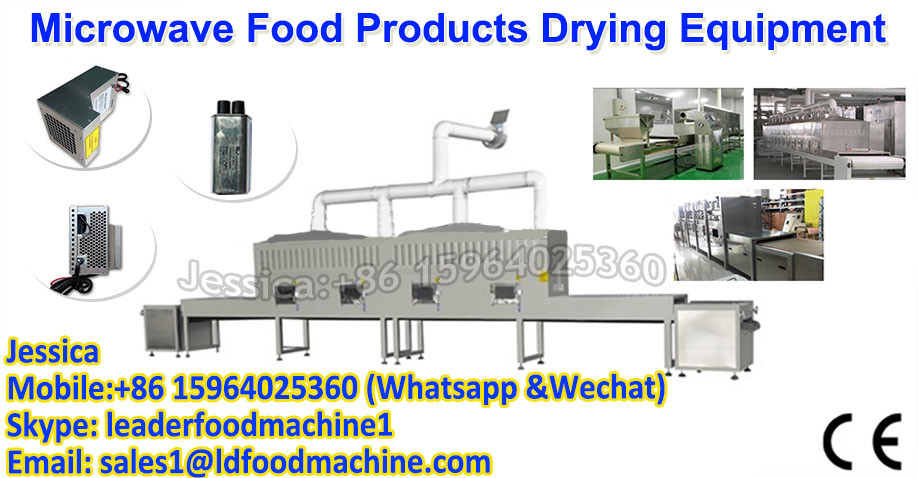