oilve oil refining equipment
Automatic Control System of oilve oil refining equipment
Our company has applied the automatic control system with advancedness, security, reliability into the pretreatment, extraction, refining and fractionation in large oil plants. For its application in automatic control system, it can control the production in the entire workshop and monitor the operational status of each device by controlling the computer terminals in the room. One person only can operate the entire workshop, with efficient production management. It has reduced the production cost LDly and improved the management efficiency.
oilve oil refining equipment Introduction:
Alkali hot water
Crude oilâÂÂfilterâÂÂmixâÂÂreactorâÂÂmixâÂÂreactorâÂÂcentrifugal separationâÂÂoil residue
â âÂÂ
Phosphoric acid hot waterâÂÂmix âÂÂ
âÂÂ
degumming oilâÂÂcoolerâÂÂdryâÂÂcentrifuge separationâÂÂmixâÂÂalkali liquor
â âÂÂ
â vacuum steam jet pumpâÂÂsteam citric acid
â âÂÂ
bleaching earthâÂÂmixâÂÂdecoloringâÂÂfilterâÂÂdecoloring oilâÂÂmixâÂÂheat
âÂÂ
refined oilâÂÂfilterâÂÂcoolâÂÂdeodorizingâÂÂvacuum
oilve oil refining equipment-Main Processes Introduction
oilve oil refining equipment
Neutralization: the crude oil is output by the oil feed pump from the oil tank, and next enters the crude oil heat exchanger to recover part of heat after metering and then is heated to the required temperature by the heater. After that, the oil is mixed with the metered phosphoric acid or citric acid from phosphate tank in the gas mixture (M401), and then enters the conditioning tank (R401) to make the non-hydratable phospholipids in oil change into the hydratable phospholipids. Add the alkali for neutralization, and the alkali quantity and alkali solution concentration depend on the quality of the crude oil. Through the heater, the neutralized oil is heated to the temperature (90ðC) suitable for centrifugal separation to remove the phospholipids, FFA and other impurities in the crude oil. Then the oil goes to the washing process.
Washing: there is still about 500ppm soap in the neutralized oil from the separator. To remove the remaining soap, add into the oil about 5~8% hot water, with water temperature 3~5 ðC higher than the oil generally. To achieve more stable washing effect, add phosphoric acid or citric acid when washing. The re-mixed oil and water in the mixer is heated to 90-95ðC by the heater, and then enters the wash separator to separate the remaining soap and most water. The water with soap and oil enters into oil separator to separate out oil in the water. Further catch the oil outside, and the waste water is discharged to the sewage treatment station.
Vacuum drying stage: there is still moisture in the oil from the wash separator, and the moisture will affect the stability of the oil. So the oil at 90ðC should be sent to vacuum drier to remove the moisture, and then the dehydrated oil goes to the decoloring process. Finally, pump out the dry oil by canned pump.
Decoloring Process:
The main function of decoloring process is to remove oil pigment, residual soap grain and metal ions. Under negative pressure, the mechanical mixing method combined with steam mixing will improve the decoloring effect.
Picture of oilve oil refining equipment
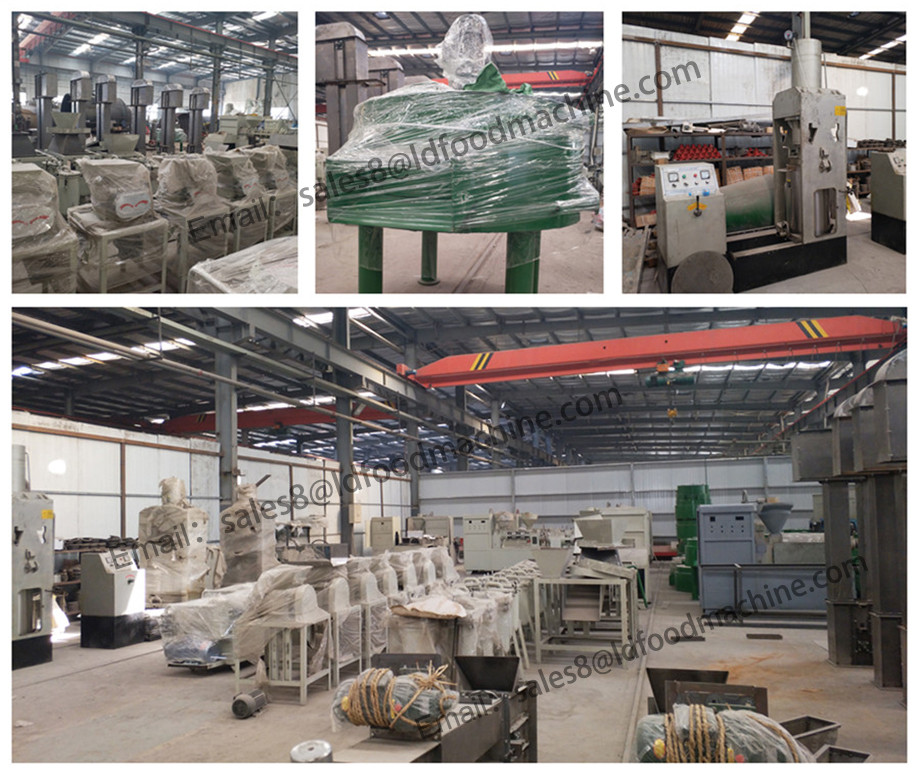
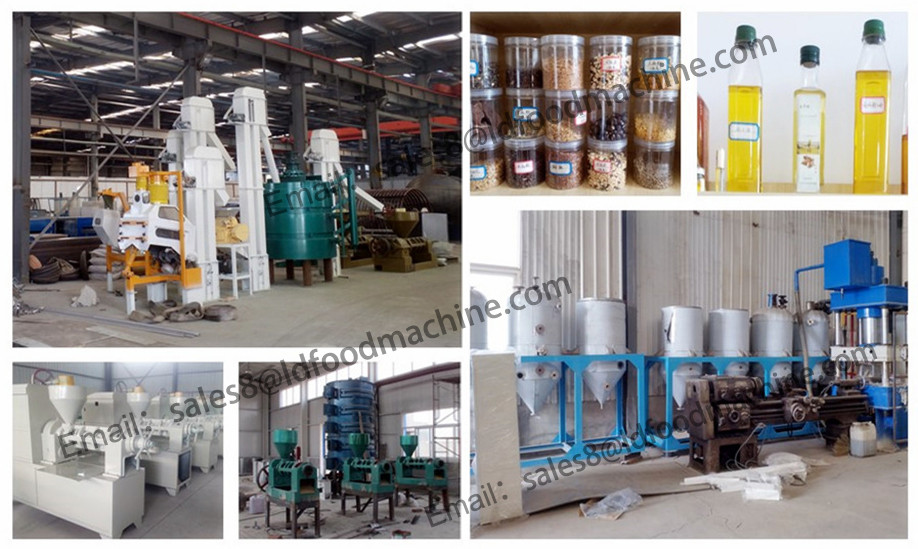
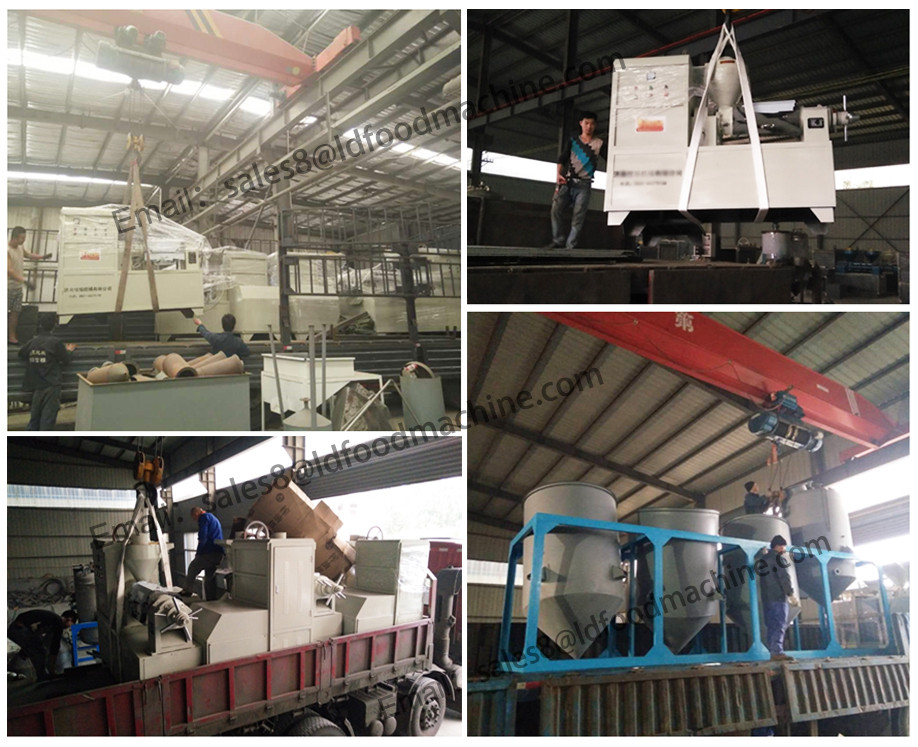
If you have interest in our oilve oil refining equipment,just free to contact us.