100 ton cotton solvent extraction
Product Description
Palm fruit, palm kernel, coconut, cashew, avocado, tiger nut, peanuts, rapeseeds, soybeans, castor oil plant, sesame seeds, benne seeds, sunflower seeds, cotton seeds, tea seeds, Tung seeds and ,grape seed etc.
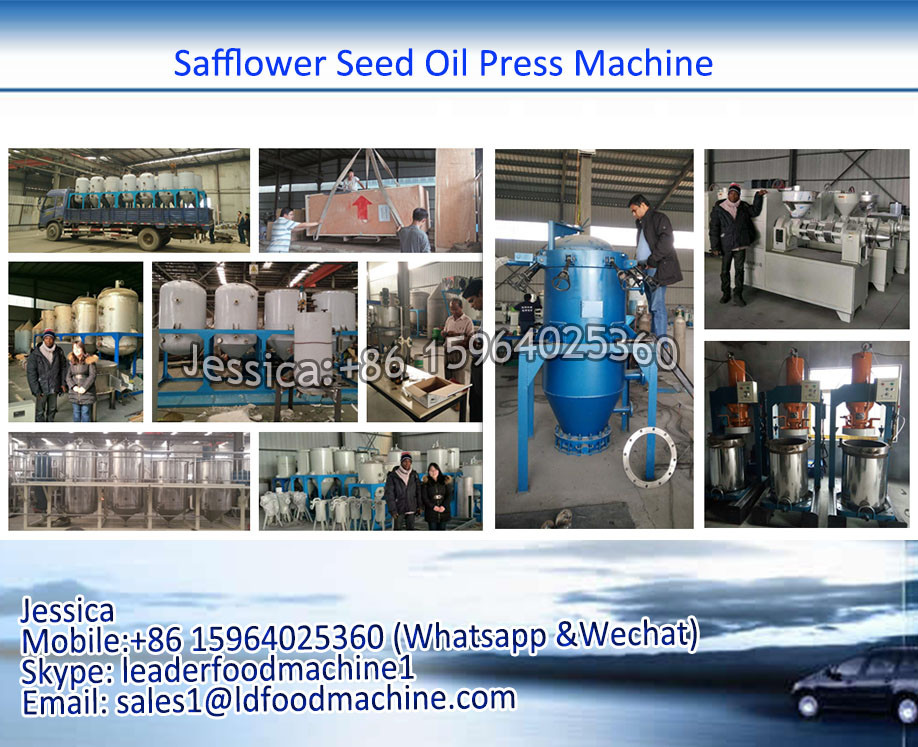
Solvent Extraction Processing
1. One is wet meal . The meal has the moisture and solvent . Then we need to Desolventizing this . Keep the olvent at 500ppm in the cake ,and moisture is 12.8-13.2 % .
2. Another is Miscella . Then the miscella has much solvent and impurities . We also need to wipe off the solvent and impurities. Then we can get the second grade oil .
3. Third part is solvent recycle . After we make the solvent change vapor , Then by the condensor , we recycle use the solvent oil . It can save our cost .
4. Paraffin oil recovery process .This process is main recycle solvent that canot cooled .
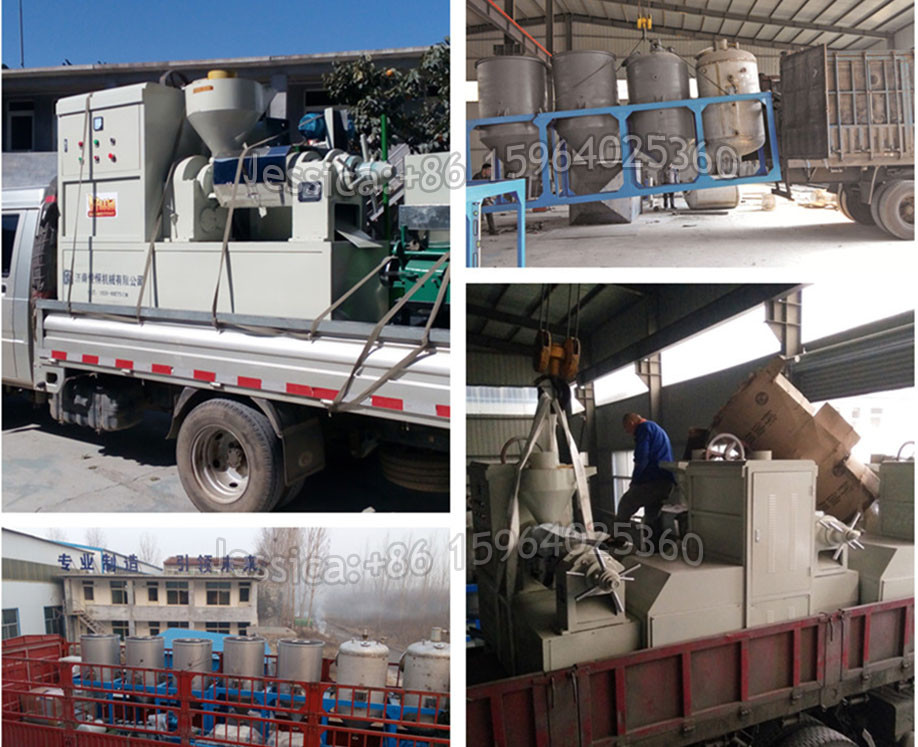
1. Adopt stainless steel fixed grid plate and increase the horizontal grid plates, which can prevent the strong miscella from flowing back to the blanking case, so as to ensure good extraction effect;
2. Its rotocel extractor is driven by rack, with unique rotor of balanced design, low rotating speed, low power, smooth operation, no noise and quite low maintenance cost;
3. The feeding system can adjust the rotating speed of airlock and main engine according to the feeding quantity and maintain a certain material level, which is beneficial to the micro negative pressure inside the extractor and reduce the solvent leakage.
4. The advanced miscella circulation process is designed to reduce the fresh solvent inputs, reduce the residual oil in meal, improve the miscella concentration and save energy by reducing the evaporation capacity.
5. The high material layer of the extractor helps to form immersion extraction, reduce the meal quality in miscella, improve the quality of crude oil and reduce the evaporation system scaling.
Specially suitable for the extraction of various pre-pressed meals.
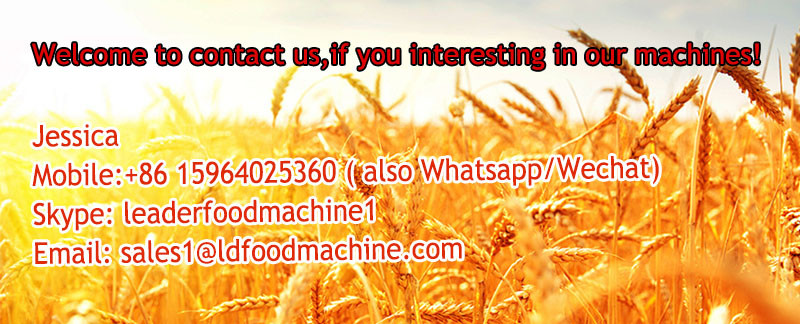
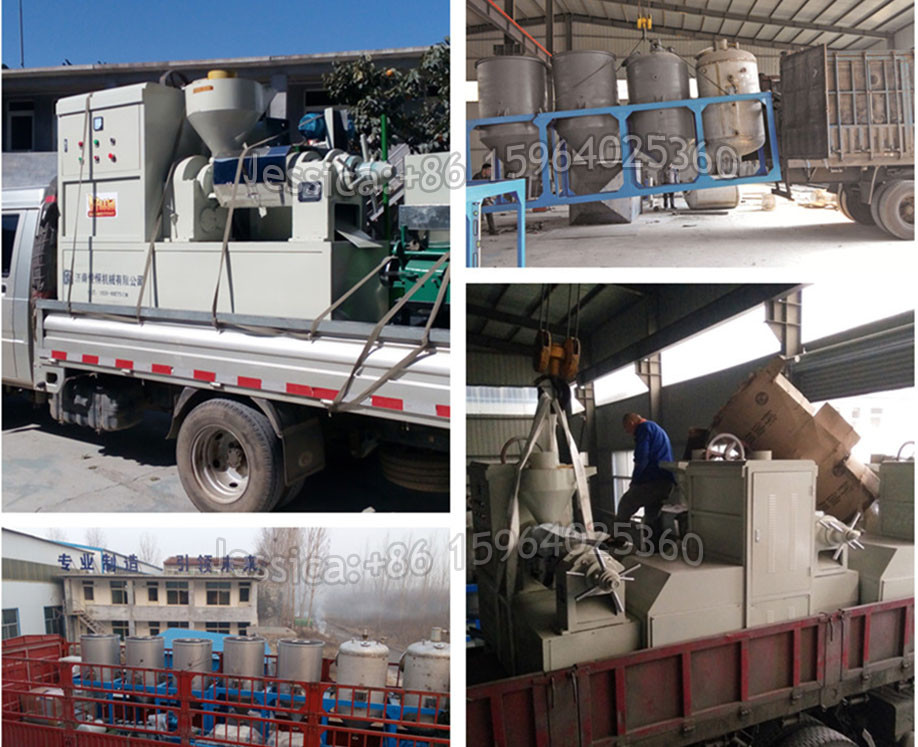
The desolventizer has the three layers , the first layer is pre - desolventizing layer . The second layer is ventilating layer .
The third is desolventing layer . The fourth layer is drying layer . The fiveth layer is cooling layer .This process of pre - desolventizing , we use the indirect steam to heat , the tempreature is 70 -80degree .
Then the cake enter the ventilating layer , the size of hole is 25 to 30 mm , the we can open the hole by the steam , which make us easily make the solvent evaporate .
The Desolventing layer , the temperature is 107- 108 degree ,this layer , we main desolventize the solvent by the superheated steam .
Then the cake enter the drying layer , the process , its temperature is 110 - 120 degree , and this process we can make the moisture is 12.8-13.2 in the meal .
Then the cake entre the cooling layer , cooling the temperature to understand 40 degree . And in the meal , the solvent residaul is less than 500 ppm
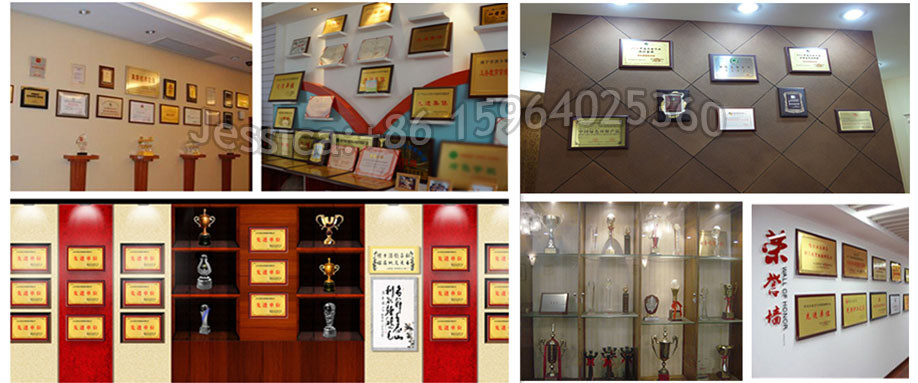
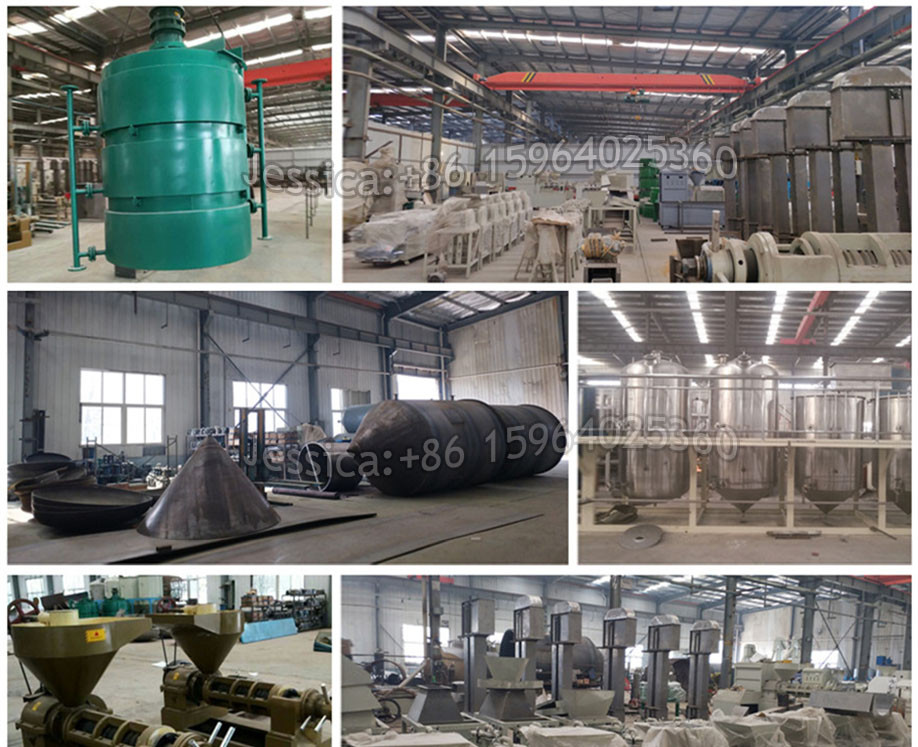
Company Information
Our company
If you are intrested in our product, please contact me directly!!